
Transferring Your Injection Mold to Maintain Production
Move from headaches to happiness by transferring your mold, finally receiving reliable and consistent production
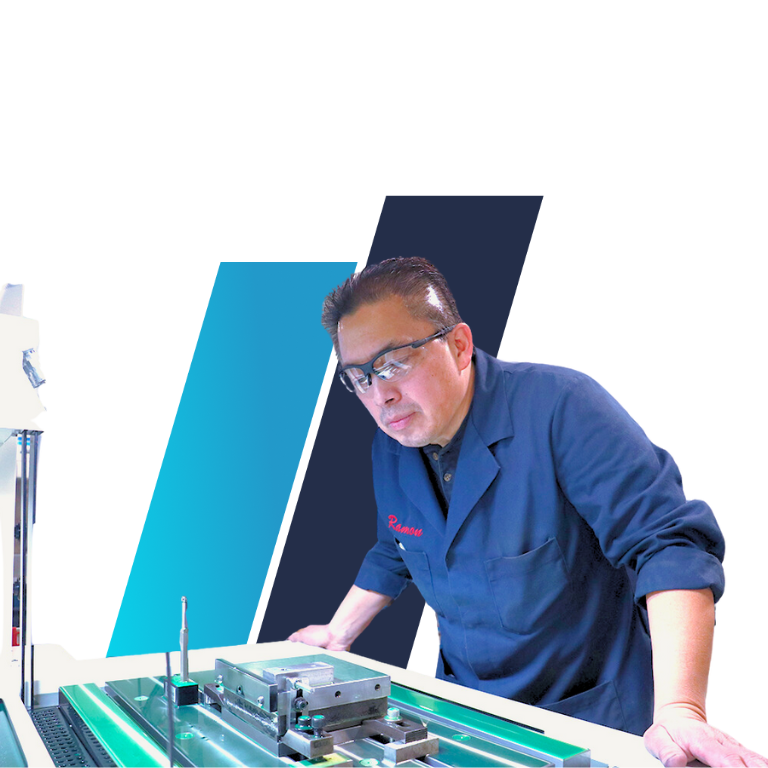
Ensuring Optimal Performance and Longevity for Your Transferred Molds
We conduct a detailed mold review process to ensure your transferred molds function efficiently and extend their lifespan.
We thoroughly assess the mold assembly to uncover and fix hidden issues that impact performance.
Identifying and addressing potential damage can restore mold functionality and avoid unnecessary replacement.
We analyze each mold component’s movement to ensure proper operation and interaction within the system.
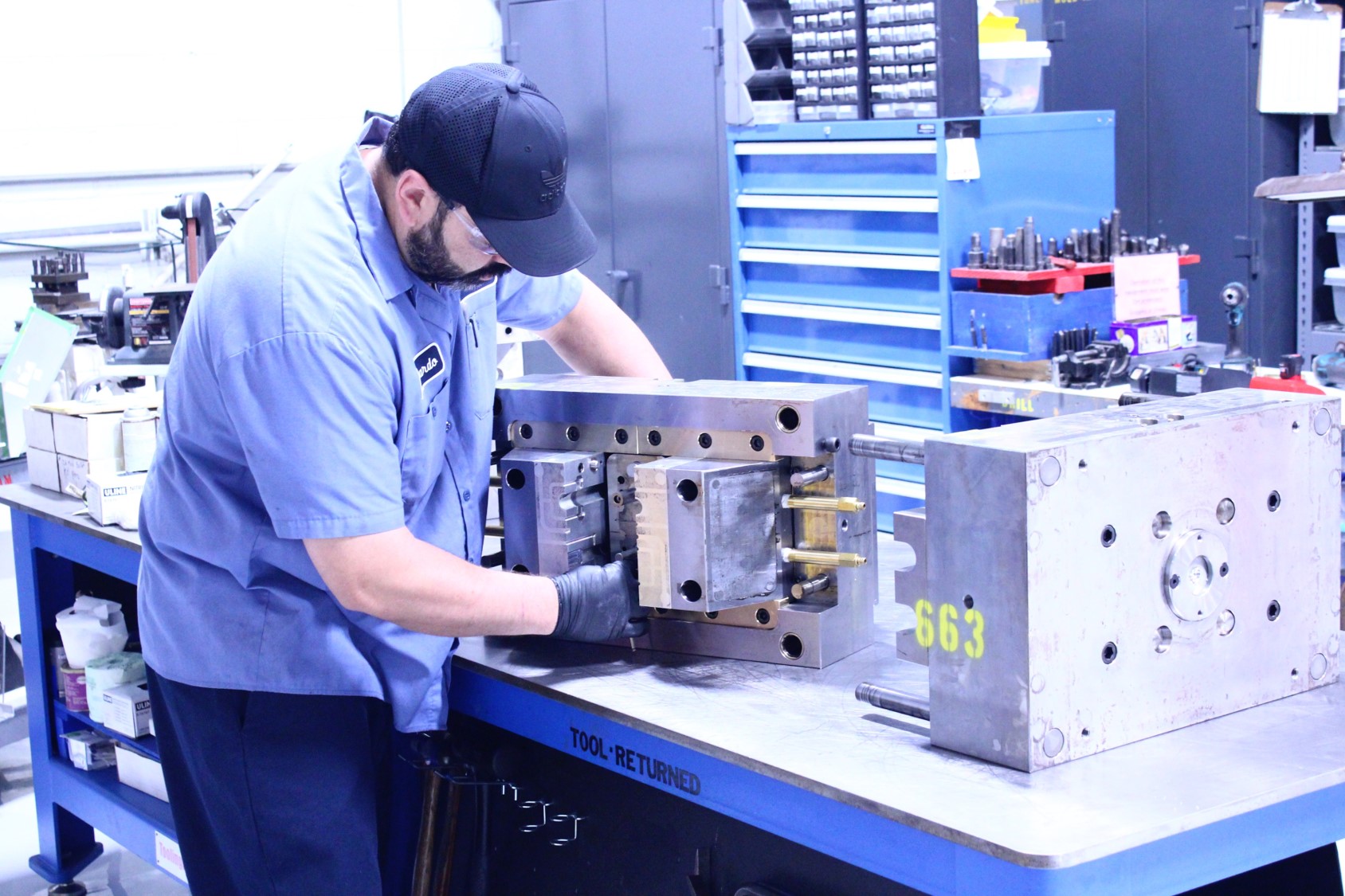
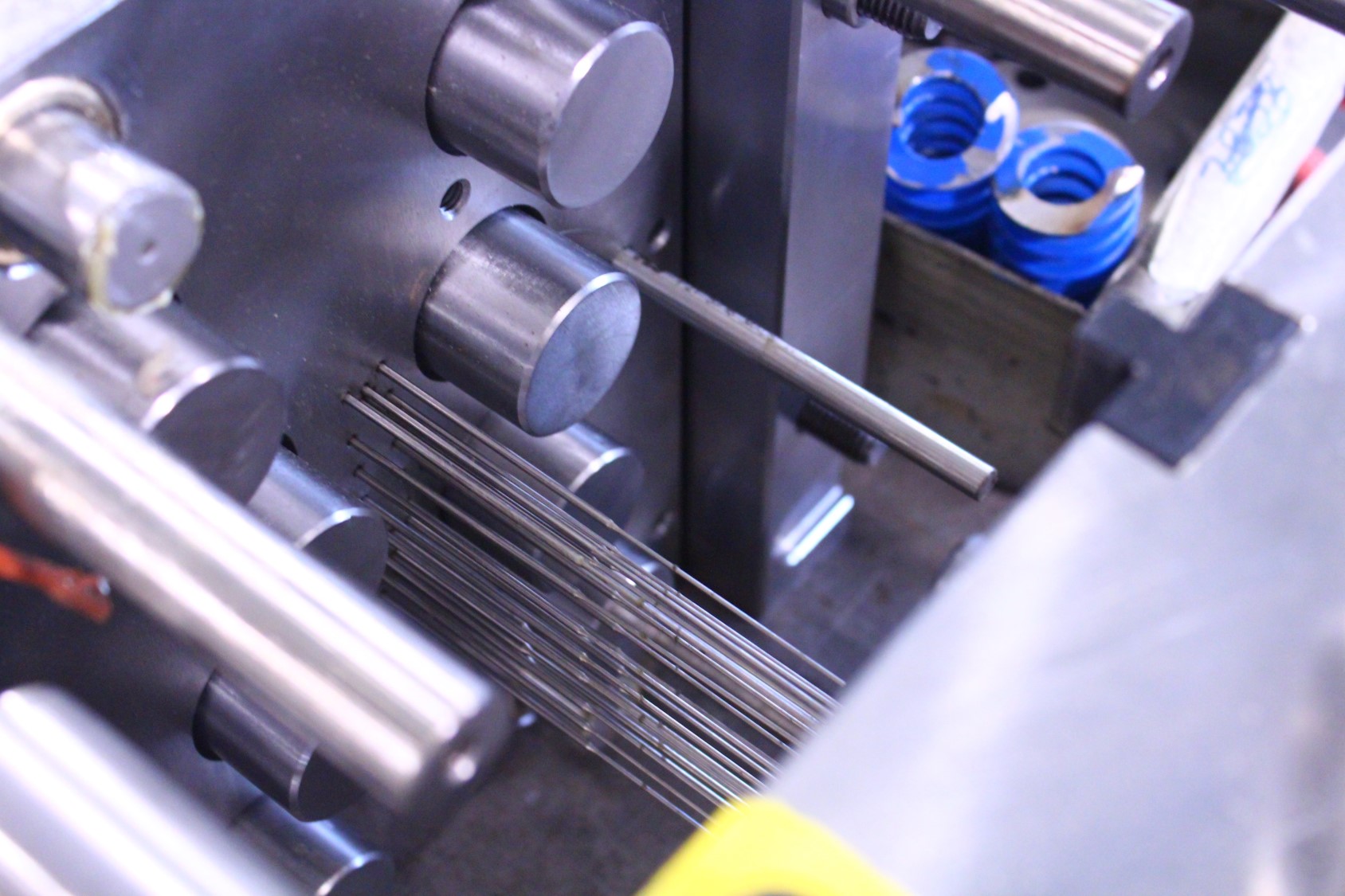
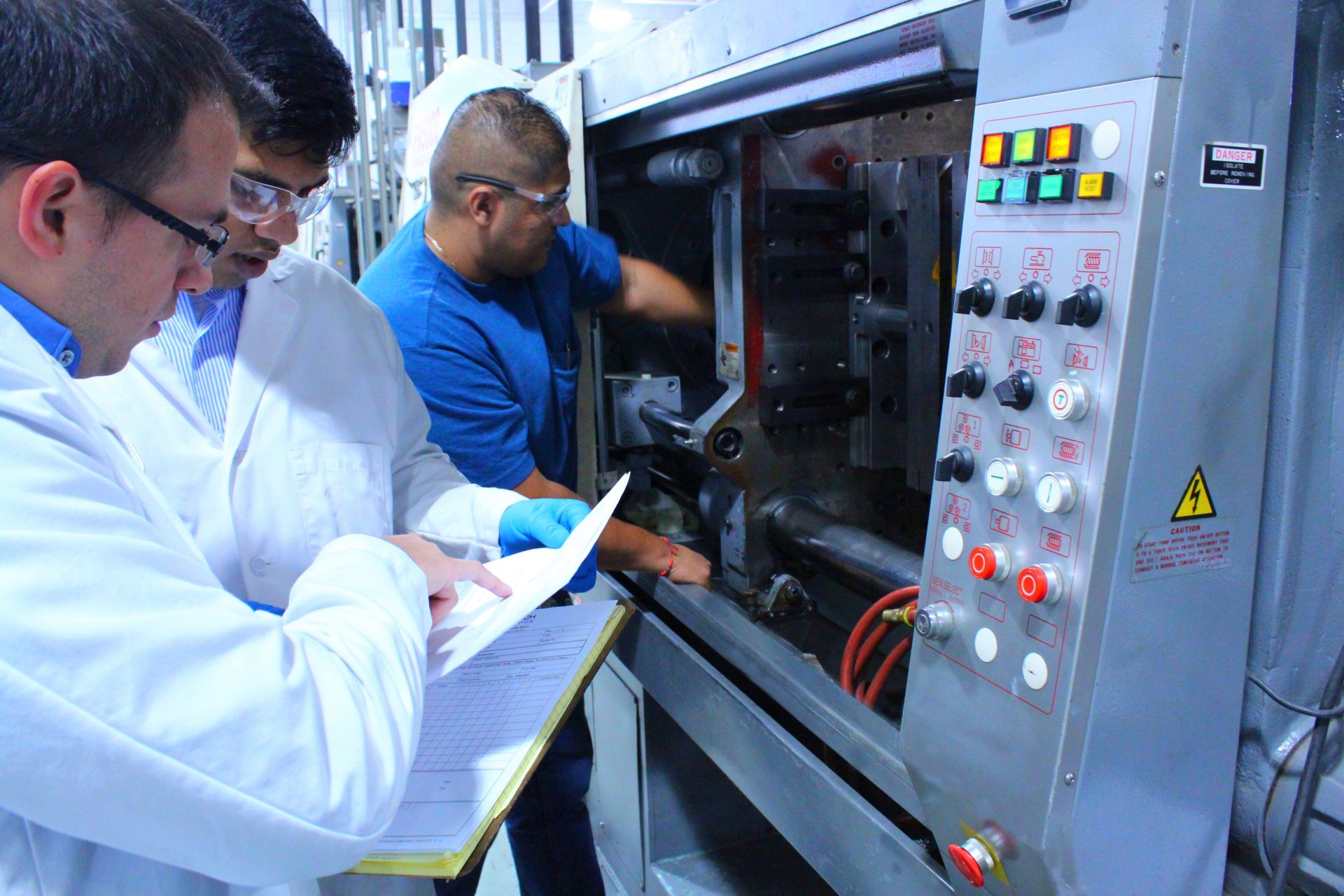
Benefits of a Proper Mold Transfer
A well-executed mold transfer process goes beyond simply relocating a tool—it ensures long-term success in production.
Read more about the mold transfer process in this comprehensive article:
Key Benefits:
- Minimized Production Downtime
- Extended Mold Life
- Consistent Part Quality
- Reduced Long-term Costs
- Improved Production Efficiency
- Risk Mitigation
- Pad Printing and Labeling
Mold Transfer FAQs
A mold transfer occurs when an injection mold is moved from one manufacturer to another. It’s often done to improve production quality, reduce costs, or when the original manufacturer can no longer meet production needs. During the transfer, the new manufacturer assesses the mold’s condition to ensure it can operate efficiently in the new environment.
You might consider a mold transfer if your current manufacturer is unable to meet your production demands, if you’re looking for better service or lower costs, or if you’re consolidating suppliers. A mold transfer can also occur if a manufacturer goes out of business or your project has grown beyond their capabilities.
The main risks include damage to the mold during transport, undetected wear or damage from previous runs, and incomplete knowledge of the mold’s design or history. These issues can lead to production delays or defects if not properly addressed. That’s why a thorough inspection and testing process is crucial during the transfer.
Natech uses a detailed mold review checklist to identify any potential issues with the mold before it enters production. Our mold transfer experts thoroughly inspect each component, correct any misalignments, and conduct test runs to ensure the mold functions as expected. We also provide regular updates to keep you informed of any findings and necessary repairs.
The length of a mold transfer depends on the complexity of the mold, its condition, and the level of repairs or modifications required. A simple mold with no major issues may take just a few weeks, while a more complex or damaged mold may require a longer transfer and remediation process. At Natech, we work to minimize downtime and provide a clear timeline based on the mold’s specific needs.
Yes! During the transfer, our team can identify areas for improvement, such as optimizing the mold design, enhancing performance, or increasing the mold’s lifespan. These upgrades can help reduce defects, improve efficiency, and ensure higher-quality parts.
Natech accepts a wide range of molds for transfer, including those used in medical, pharmaceutical, diagnostic, and consumer product applications. Whether your mold is simple or complex, we have the expertise to manage the transfer and ensure seamless integration into our production processes.
Mold maintenance is a key part of ensuring long-term production success. Even if your mold passes the initial inspection, regular maintenance is recommended to keep it running smoothly and avoid unexpected breakdowns. Natech provides ongoing mold maintenance services to extend mold life and maintain high-quality output.
Load more questions
Read our Medical Device Design Case Studies
Driven by Collaboration, Fueled by Continuous Improvement