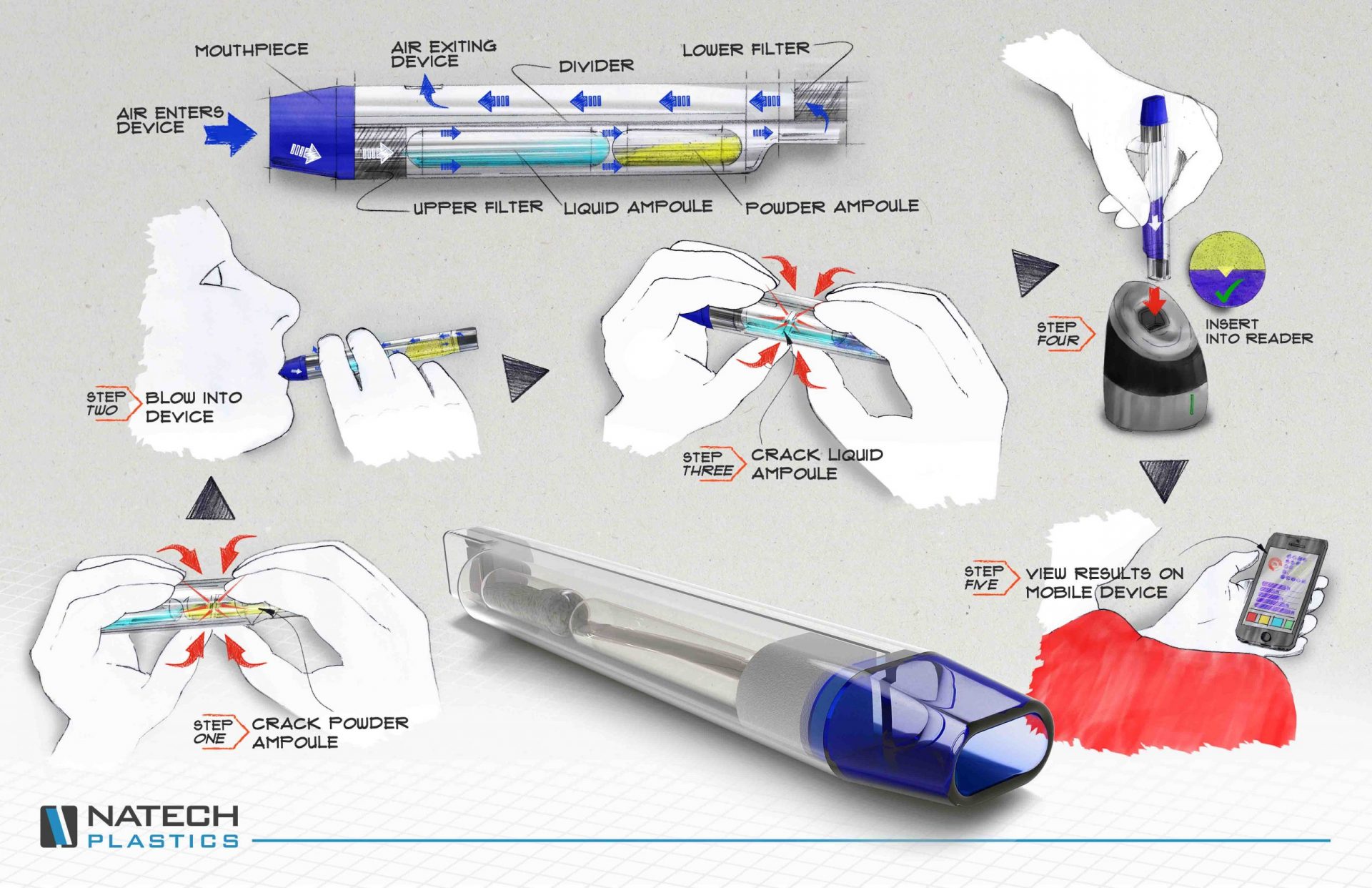
Quality by Design
As I sat through the presentations at this year’s Molecular Med Tri-Con on molecular medicine and diagnostics, I was impressed by the recurring theme of manufacturability. As I have said many times, skipping this step early in the process introduces risks later in the life of the product. The industry still has a ways to go, but the good news is that we are making progress. ISO, cGMP, and other standards have helped raise awareness for the best practices in quality. Designing for manufacturability and assembly designs quality into the product versus just inspecting quality into the product. Quality by Design requires a quality mindset, risk-based thinking, and systems thinking.
Quality Mindset
The important point that many novices and even many experienced clients do not understand is that increasing quality actually lowers risks, it lowers costs, it saves time in the long run, and ultimately higher quality leads to higher sales. This was true when Deming taught quality in Japan during the 1950s, and it is just as true today.
This is because quality errors, rework, troubleshooting, and delays have direct costs as well as indirect costs. The direct costs of labor and rework are more apparent. The opportunity costs from diverting talent and other resources to deal with errors are less obvious. The clients and future business lost due to quality issues are unknown yet just as real and can be more impactful than all others combined.
Risk-Based Thinking
The 2015 update to the ISO 9001 standard gives great importance to risk-based thinking. Designing quality into the product requires a feedback loop which incorporates 1) the end use as well as 2) the manufacturing process. The major risk breakdowns of the Failure Mode Effects Analysis (FMEA) can be bucketed into these two areas.
Selling low-quality products introduces reputational risk. Recovering from a reputational hit poses a daunting challenge. Identifying potential manufacturing challenges is the heart of Design for Manufacturability. Reducing the number of components reduces the number of assembly errors, the number of join failures during use, the overall manufacturing costs, and the costs of quality failures. From a risk perspective these are production risks, operational risks, and financial risks. Improving quality decreases both the likelihood of a risk occurrence as well as the impact if the risk does occur.
Systems Thinking
Systems thinking is a mindset of looking at the broader picture to understand how the complex interactions of the various parts interact to maximize contribution to the performance of the whole system. All too often I see clients’ blinders point toward the objective of just hitting the next project milestone as efficiently as possible at the expense of the greater picture.
In practice, continual improvement of product design tends to happen in an iterative fashion based on feedback:
Design, Feedback;
Design, Make, Feedback;
Design, Make, Use, Feedback;
Design, Make, Use, Sell, Feedback;
and back to Design again.
This cycle of continual improvement has appeared in many variations (Shewhart’s cycle, Deming’s wheel, Juran’s loop), and the major concepts hold across the board. Unless the same person designs, makes, uses, and sells the product as artisans and craftspeople do, the gap must be bridged through connections across functional areas. This entails communication and education. As these connections deepen, the organizational mastery of Quality by Design increases.
Quality by Design can only happen with a quality leadership who sets up the support systems and group dynamics for these connections to happen. When top management links the quality mindset with risk-based thinking and systems thinking, they create the necessary platform for their team to design quality into the product.