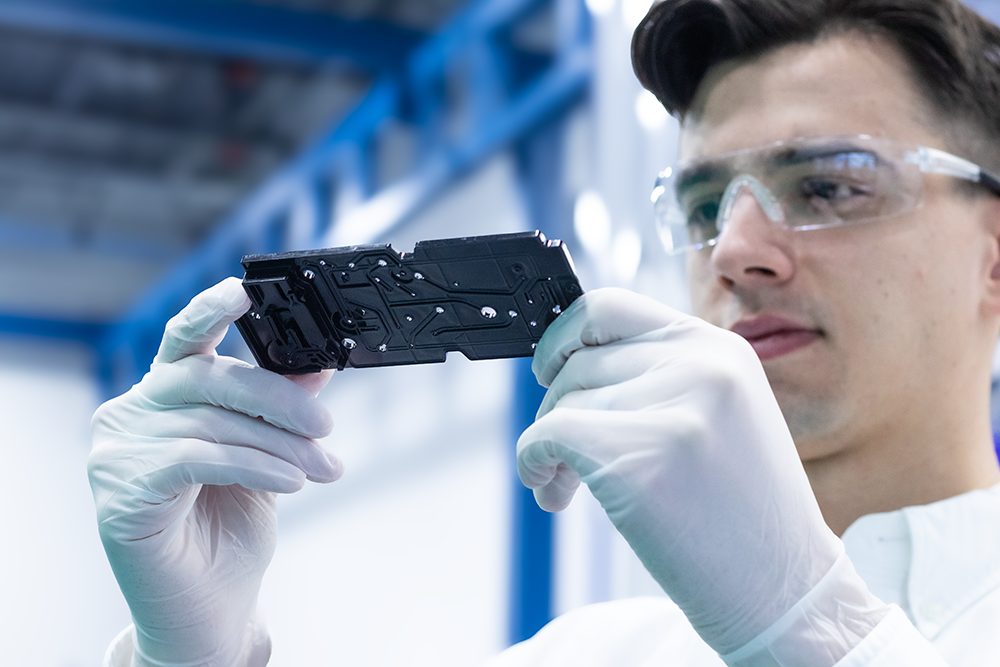
The Startup’s Guide to Injection Molding
What is injection molding, how much does it cost, and is it right for your project?
What is Injection Molding?
One of the biggest hurdles for entrepreneurs and startup leaders to overcome is understanding how their product is going to be manufactured. Injection molding is a common option for most products, and plastic injection molding is a great choice for companies looking to make thousands to millions of a specific part.
In general, injection molding is a manufacturing process that allows you to make a large number of parts in succession. It consists of injecting melted plastic into a steel mold inside of an injection molding machine. Inside the machine, the plastic melts and forms to the mold. When the mold opens the plastic part drops onto a box or conveyor, and the process repeats itself to continue to make more of that part.
In the United States alone, there are thousands of injection molding companies. One consideration for companies looking to launch products is where to have their product made. Selecting an injection molder for your product is its own process. Read more about choosing the right manufacturer here.
The Process for Having Your Part Injection Molded
Like any manufacturing process, preparing to have your product injection molded starts well before you are ready for manufacturing. In short, there are five major stages that occur.
1. Initial Product Design
This varies from product to product. For some, this can be the sketch on a napkin, while others begin with a more detailed CAD drawing. Either way, the initial design, with dimensions, functional, and quality requirements is the starting point for your injection molded part.
2. Prototyping
Before you can begin manufacturing, there needs to be some level of prototyping. Before you hit this stage, it is best to consult with potential injection molding partners. They will be able to guide you in selecting various methods and suppliers for prototyping. For some, this may be 3D printing sample parts, while others may need prototype tooling and manufacturing of a small number of parts to understand product risks and functionality.
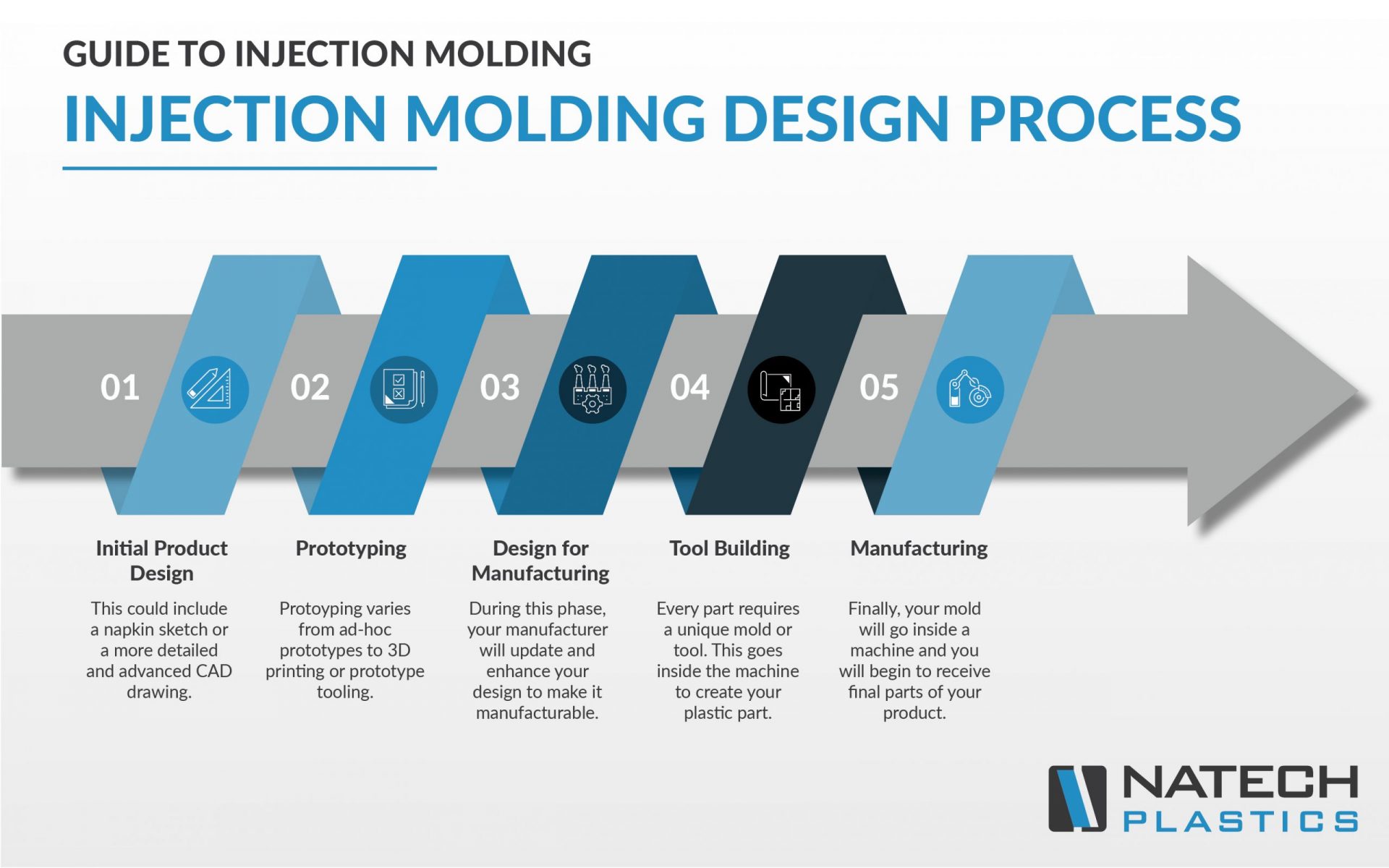
3. Design for Manufacturing
The design for manufacturing (DFM) phase is one of the most critical in your injection molding process. During this phase, your injection molding expert will work with your team and your product design to prepare it for manufacturing.
Design for Manufacturing includes reviewing a detailed DFM checklist and product requirements outline. Injection molding design requires expertise in understanding risks, product aesthetics, and user interface. This step will help in material selection and mold selection as well.
4. Tool Building
All injection molded parts require its own unique mold or tool. This is an aluminum or steel mold that is specially made for your product. Selecting the right mold is crucial for your immediate and long-term project success.
Your mold is what goes inside the injection molding machine to create your part. It is one of the largest upfront costs in your injection molding process. Depending on which mold you select, this can create anywhere from thousands to millions of parts for you. Your injection molding partner may have an in-house mold builder or will use trusted suppliers to make sure you have a tool that will last you into the future.
5. Manufacturing – Injection Molding
After all that, you are finally ready to manufacture your part. Your mold will be installed in an injection molding machine and parts will begin to be produced. After your parts are manufactured, you will work with your contract manufacturer on any assembly, packaging and shipping needs.
It is also during this stage that you will receive detailed quality outlines of your part, including first article inspection reports (aka dimensions and outlines of the first officially manufactured parts), and additional quality specs depending on your application. Depending on the number of parts you need, you will have parts beginning to ship to you shortly after you begin your production run.
Top 5 Benefits of Injection Molding
Injection molding is one of the most commonly used methods of producing identical plastic parts.
1. Ability to produce at low and high-volumes
Utilizing injection molding allows you the ability to produce a small volume of parts (a few hundred) to a very high number of parts (tens of millions), all using the same process.
2. Creating parts with highly detailed & complex geometry
Injection molding allows you to create parts that are extremely detailed and/or have extremely complex geometry. This manufacturing process allows you to create a part that looks and functions as you imagine while maximizing process efficiency.
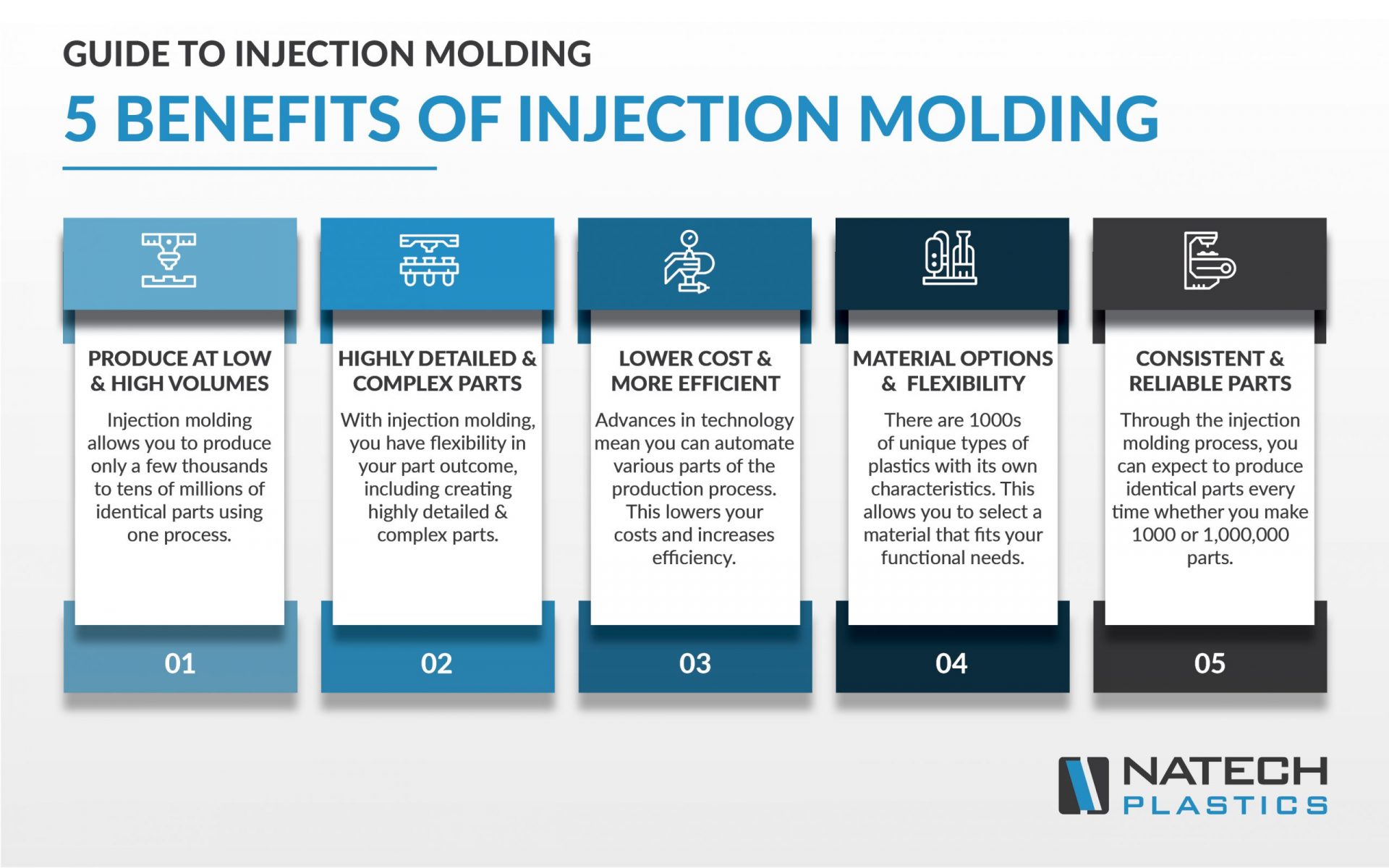
3. Lower costs and greater efficiency through automation
Advances in technology now make it possible to automate many parts of the production process. This includes everything from taking parts out of the mold, to de-gating the part to assembly. All this equals lower costs from removing direct labor from your process and greater efficiency from a reliable and expedited process.
4. Material selection and material flexibility
While there are seven main categories of plastics, there are actually thousands of unique types of plastics, each with its own unique composition and characteristics. Additionally, different types of plastics can be combined with other plastics or additives to achieve a specific end result. This means whether you need strength and rigidity, clarity and flexibility, or antimicrobial or biodegradable properties, there is a plastic material that can fit your need.
5. Consistency and reliability in your parts
Injection molding itself is designed to create consistent, identical parts every time. This means that whether you plan on making 1,000 or 100,000,000 million parts, you can expect to see the same part every time. This level of reliability allows you to breathe easy knowing you have quality and consistency on your side.
How Long Does Injection Molding Take?
While injection molding is one of the most efficient and cost-effective methods for producing your plastic part, it does take time. Each stage in the process has a varied timeline, and you should work in concert with your manufacturer to develop a timeline that meets your needs and sets expectations.
Design for Manufacturing
4 hours – 60 hours
Regardless of your product design, some amount of design for manufacturing will need to take place prior to being about to build a mold to create it. Depending on your design and your application, this can include just a few hours of design and engineering work, to more than 60 hours of design updates.
Tool Building
2 weeks – 12+ weeks
Part complexity, mold cavitation, and mold material are the primary factors in your tool building lead times. Simple, single cavity aluminum molds can be produced in as little as two weeks, while highly complex, high cavitation, class 101, hardened steel molds can take several months.
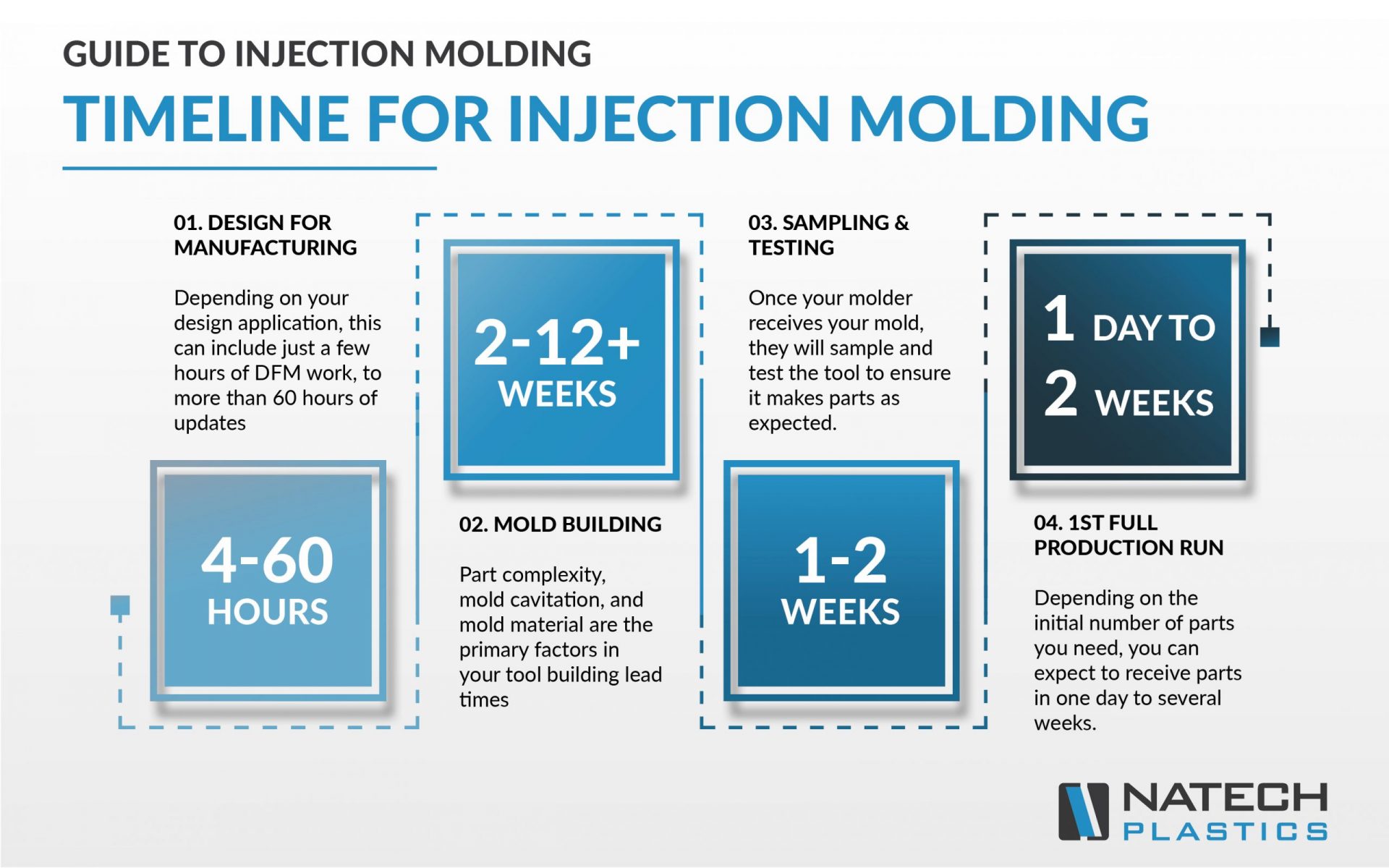
Sampling and Testing
1 week – 2 weeks
Once your manufacturer receives your mold, they will need to sample and test the tool to ensure it makes parts as expected. They will produce a very small number of parts, test them for functionality and quality, and ask you to approve the parts. This process can take about 1-2 weeks, depending on the current schedule of your manufacturer and the level of testing needed for your part.
First Full Production Run
1 day – 2 weeks
After you have approved the samples of your part, your manufacturer will put your mold on their schedule and begin to run production. Depending on the initial number of parts you need, you can expect to receive parts in as little as one day or as long as a few weeks.
After you have your mold and your first production run is approved, getting parts is just a matter of the quantity you need and the cycle time it takes the machine to create your part. Most parts have a cycle time of less than one minute – so you can expect anywhere from hundreds to thousands of parts an hour, depending on your part complexity and mold cavitation.
How Much Does Injection Molding Cost You?
Trying to say how much it costs for injection molding is similar to asking how much it costs to buy a house – it depends. Of course, there are a few categories of cost that can help you plan and prepare for the investment. Each of these will vary depending on your specific part and project and working closely with a contract manufacturer you trust will help you better understand what your overall costs will be.
Design and Engineering
$200 – $300 / hour
Depending on when you engage your manufacturer and how far along you are in the design process, your costs will vary greatly here. As this is one of the most critical stages of your product development before building a mold, you should anticipate at least $1,000 in costs, but could go up to $10,000s.
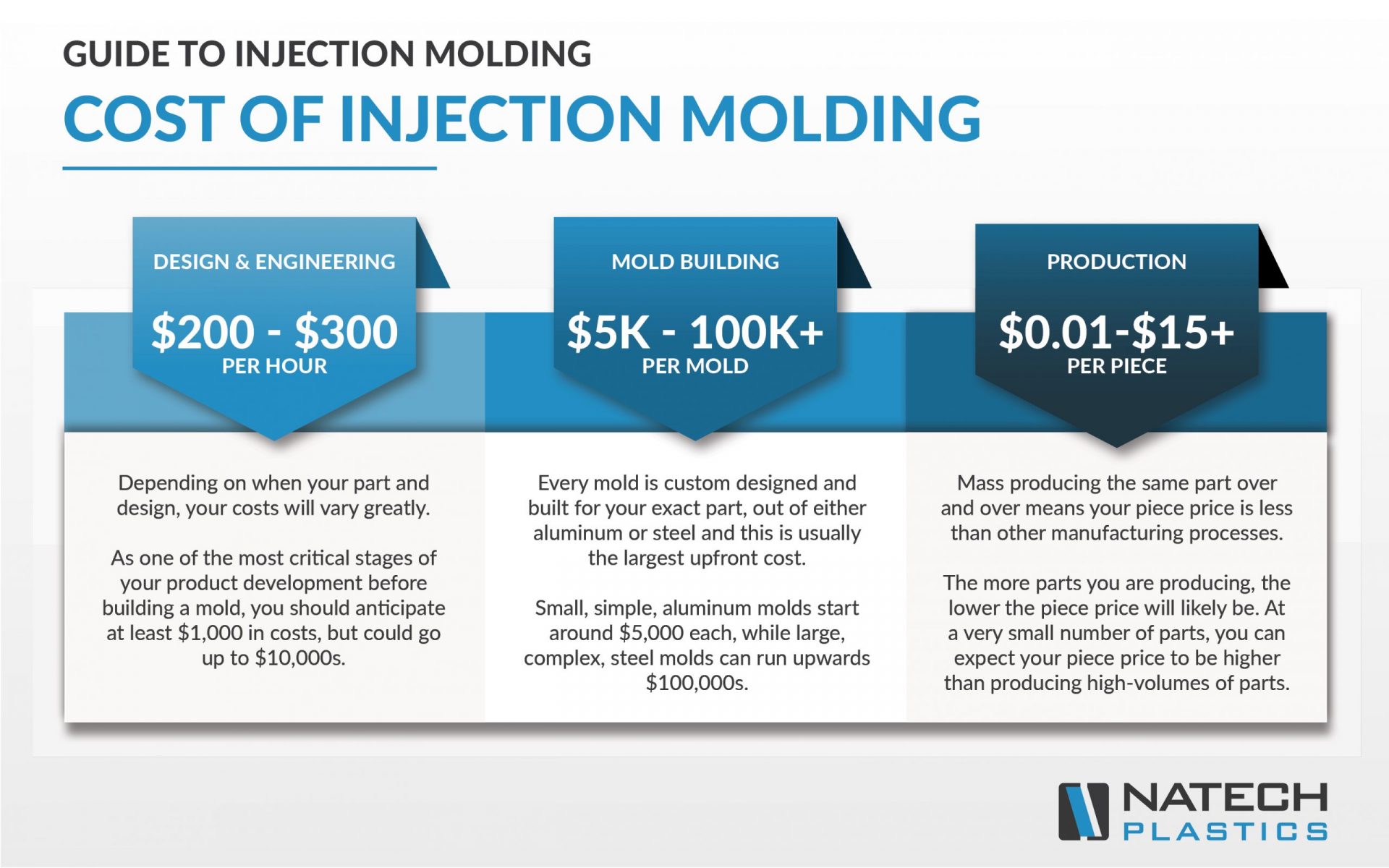
Mold Building
$5,000 – $100,000s
The biggest sticker shock for startups and entrepreneurs typically comes to the cost of building a mold. Every mold is custom designed and built for your exact part, out of either aluminum or steel. This is usually the largest upfront cost for most entrepreneurs, and it is important to be prepared.
Small, simple, aluminum molds start around $5,000 at a minimum and increase with size and complexity. Often aluminum molds are “starter” tools for production to get a small volume of parts quickly. They don’t last as long and cannot produce as many parts as higher-class molds.
Of course, that means more complex, higher cavitation and higher-class material molds can run you upwards of $100,000s. However, these molds create more parts, at a faster rate, and last for decades producing millions of parts.
Production Piece Price
$0.01 – $15.00+/part
Where injection molding really helps startups and entrepreneurs is in the piece price. Mass producing the same part over and over means your piece price is less than other manufacturing processes. The more parts you are producing, the lower the piece price will likely be.
If you are starting off producing only a very small number of parts (fewer than 100), you can expect your piece price to start around $15.00 per part. This is because you are paying for the startup costs, mold installation, the initial material purchase, etc. However, as you produce more and more parts, your piece price comes down, meaning you can be looking at part costs of pennies per part.
Is your project right for injection molding?
While injection molding is the most common production method for plastic parts, it is not right for every application. Common reasons why a startup may select NOT to use injection molding include higher upfront tooling costs, part design restrictions or the cost of producing only a very small amount of parts.
However, if you are looking for thousands or millions of parts to be produced in an efficient and consistent manner, and you are comfortable investing in building a quality mold to make your parts, injection molding should be a perfect fit for your project.
Talk to a Natech team member to see if your project is right for injection molding.