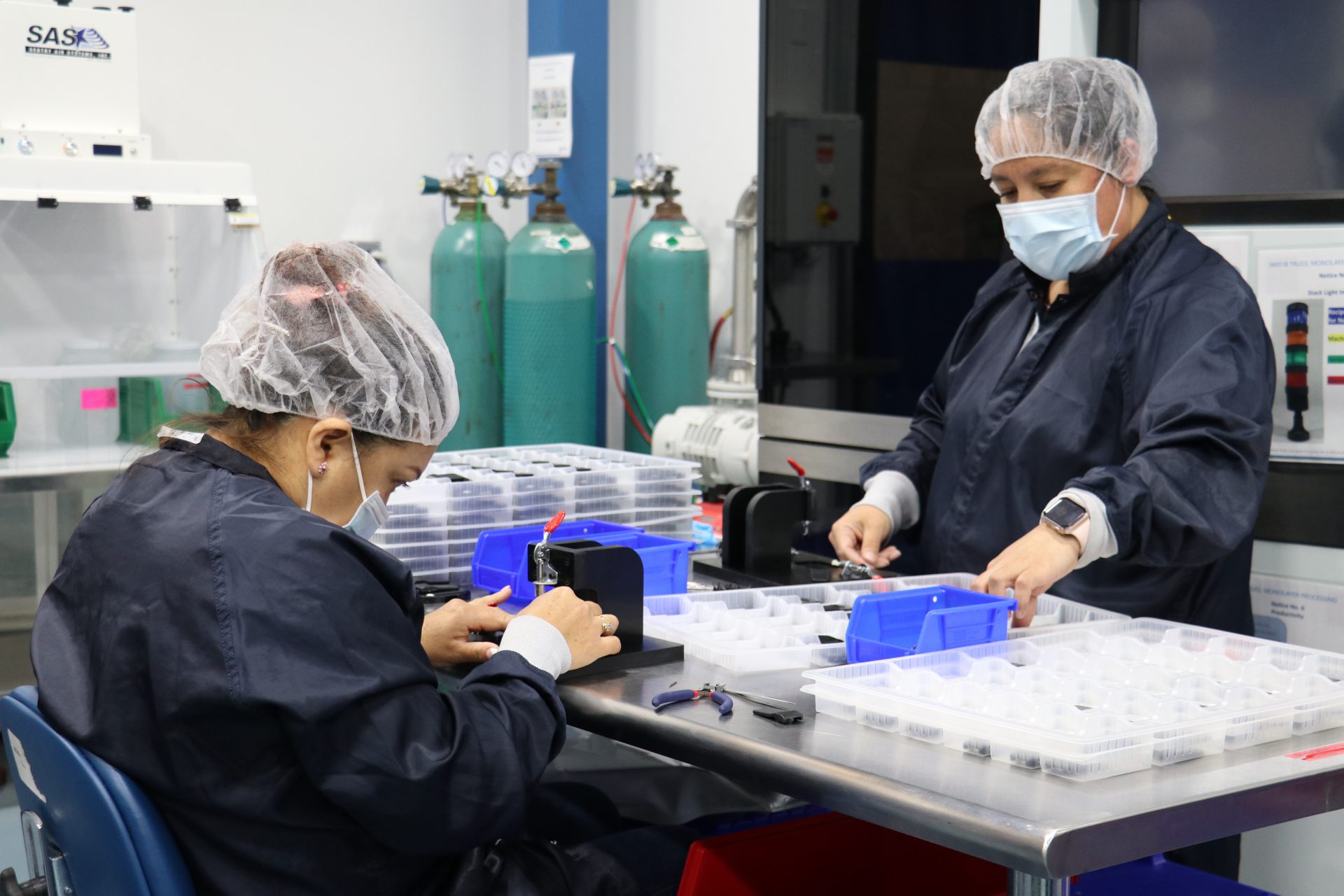
Why Design for Injection Molding?
Designing for Injection Molding is More Than Standard DFM
Clients who are new to injection molding are sometimes surprised to discover how involved the design for injection molding phase can be during their development program.
Constructing a mold is like a building construction project. Risks, changes, and schedules must all be well planned and competently managed for a successful launch of mid-to high-quantity products.
“But, it’s a simple part.”
People regularly come to us, claiming their part is simple and the design is ready to go as is. Although some injection molders might accept the request at face value and build the tool, the expert injection molder will want to know whether the designer was versed in the rules of thermoplastics and experienced in injection molding.
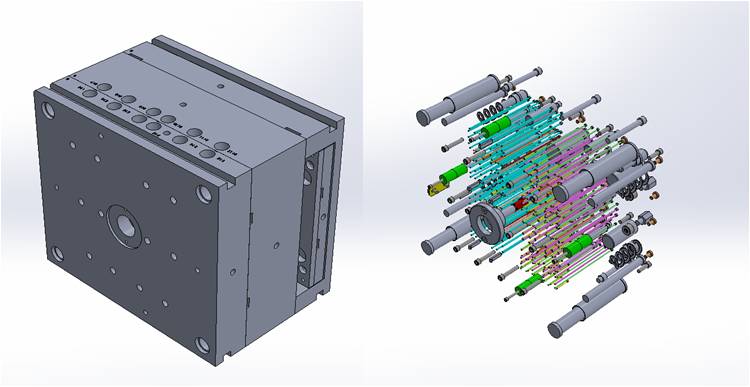
Every type of manufacturing operates by a specific set of rules and principles.
In reality, the ease with which a part may be fabricated is not a good indication of what is involved in mass production by injection molding. Clients are often surprised to discover that a simple-looking part actually requires a complex mold and a good deal of analysis to produce the right way.
“Just make it the same.“
Many clients have asked us to reverse engineer their components based solely on samples, such as machined parts or 3D printed prototypes. Sometimes we are asked to just scan another part and build a mold based on the scan. This could be like constructing a replica of a building based only on a photograph of the original.
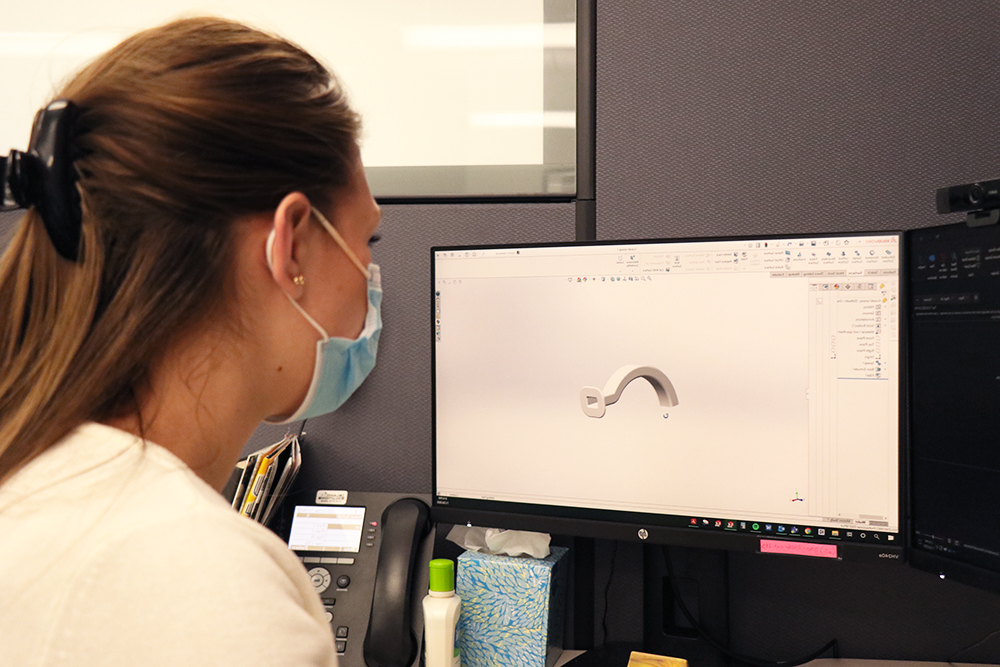
Just like buildings, molds require a lot of unseen complexity with the inner workings to properly function. The right cooling, ejection, and cam action comprise a well-built mold. Just as no two snowflakes are identical, the rules of plastics tell us that variation is to be expected from part to part. Defining upfront what “same” means is the first step.
Specific areas engineers examine during the Design for Injection Molding Phase include:
- Wall thickness and uniformity
- Amount of draft needed
- Thoughtful design of undercuts
- Structural integrity through the use of bosses or ribbing
- Material selection and type of material used
“Can’t you just do the same thing 16 times?“
When the time comes to transition from a single-cavity mold to a multi-cavity mold, some clients are surprised by the amount of planning still necessary. If the single-cavity works, constructing multi-cavity tools should require little to no planning. Right?
We all wish projects were that simple. Transitioning from a single-cavity mold to a 16-cavity mold is akin to building a single-story house versus a 16-story building. Yes, some things with the part design should have been ironed out in the single-cavity tools. The reality is that an entirely new set of design challenges, risks, and constraints must be considered for the higher cavitation mold.
Whether creating a new part, reverse engineering an existing part, or transitioning to high cavitation tooling, the design for injection molding phase is critical. The ultimate commitment is to design and build a reliably running mold.