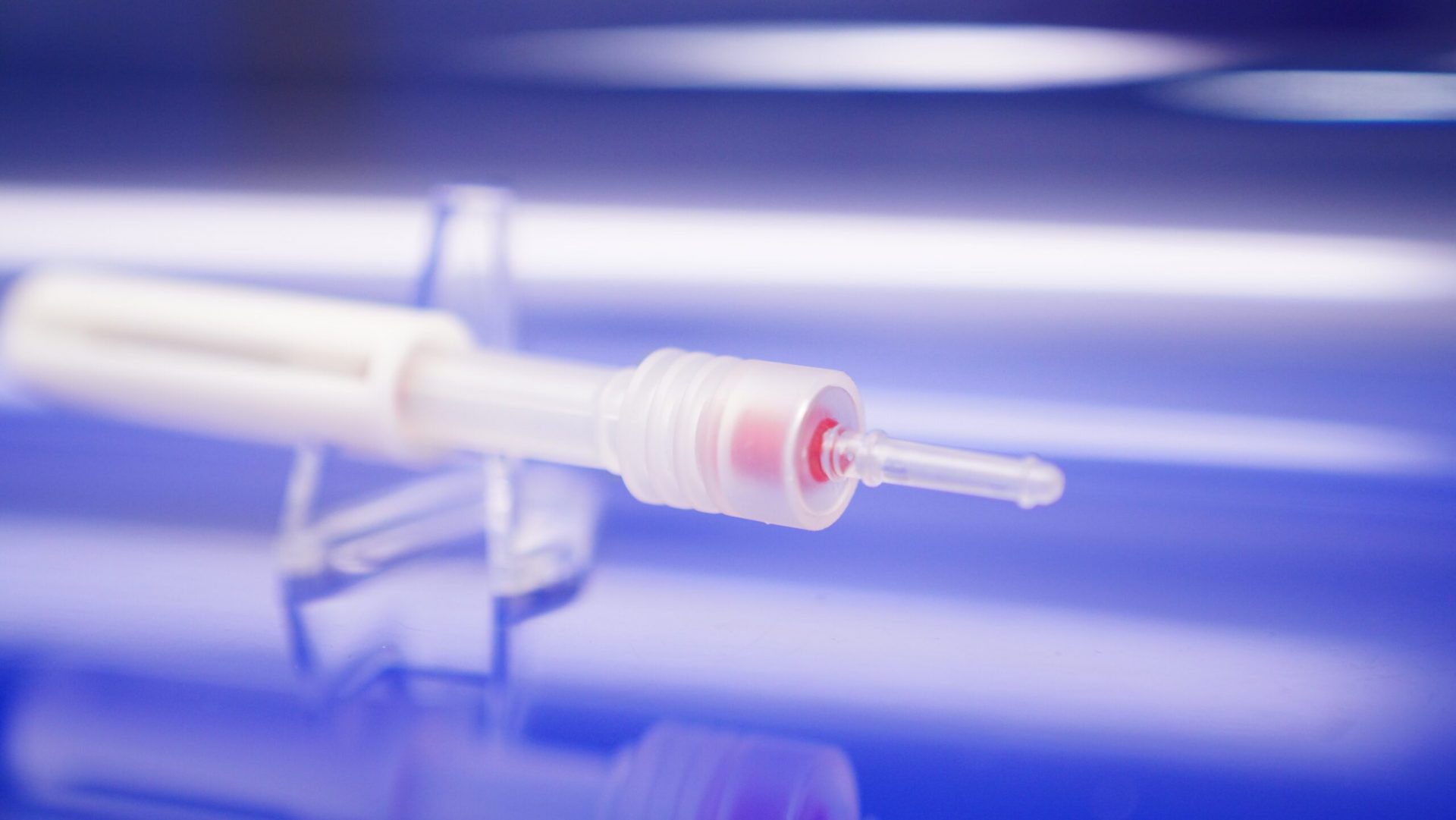
Solutions for the Top 3 Challenges in Syringe Molding
Syringe Molding: Addressing Common Challenges to Create High-Quality Products
A device that comes with a unique set of challenges is the syringe. Manufacturing custom syringes isn’t as simple as jumping from design to finished device. There are steps in between and challenges engineers need to address before a part is ready to be injection molded.
Syringes are typically made up of a barrel, plunger or piston, and sometimes a needle. Plastics are becoming more useful in medical disposables like syringes, and are more resistant to cracks, cost-effective, and sterilizable.
Syringes are devices that can be used to dispel and aspirate fluids from something. They are essential medical tools used anywhere from doctor’s offices to laboratories. Because syringes require a high degree of safety, security, and reliability, it is important that they are designed and manufactured correctly.
Top 3 Syringe Molding Challenges and Solutions
1. Achieving Low to Zero Draft
2. Maintaining Seal Throughout Stroke
3. Achieving Optimal Design
1) Achieving Low to Zero Draft
What is draft? When utilizing the process of injection molding, some part designs must be changed to include draft. Draft is used to ease part ejection from the mold. However, many syringes with long cores require near low or zero draft angles.
Why is it important? Many syringes require low to zero draftbecause the functionality of the part depends on maintaining the liquid barrier along the entire length of the part’s inner diameter. A higher draft angle could impede product functionality. Part designers must be aware of the risks of improper draft angles. Improperly designed draft angles can cause parts to improperly eject, cause the mold to be damaged, and cause the parts to be scratched.
Challenge: The challenge with low to zero draft regions is difficulty in removing the part from the mold without typical draft angles, which usually range from 0.25 degrees to 2 degrees.
Solution: In these situations, Natech engineers must carefully consider surface finish (polish), material selection, ejection method, and release agents. For surface finish and material, a high polish material is the best choice because it makes it easy to pull the part from the mold. To help remove parts from the zero draft cores, a lubricious additive may be added to the plastic resin.
Results: Choosing the right surface finish, material, and ejection method helps reduce the force needed to remove parts from the mold. Natech considers these factors when syringe molding to decrease manufacturing risks, cycle times, and overall costs, while ensuring the quality of the final syringe product.
2) Maintaining Seal Throughout Stroke
What is a seal? Seals are typically compliant components that prevent leaks and contamination of the contents of a syringe. Common seals include elastomeric pistons, overmolded components, or O-rings.
Why is it important? Seals ensure leak-proof sealing between the plunger and syringe barrel. Proper sealing allows the user to have greater control when dosing and smoother injection when using a syringe.
Challenge: The challenge with molding a gasket for syringes is maintaining a consistent, dynamic seal throughout the length of the stroke. It’s important to have a seal that doesn’t have too much interference or a seal that would make it hard for the user to push the plunger.
Solution: To address this challenge, our engineers perform tolerance stacking to make sure the outer diameter of the plunger always has an adequate interference with the inner diameter of the syringe barrel. Tolerance-stacks help engineers and designers arrive at the best specifications to ensure a tight and durable seal.
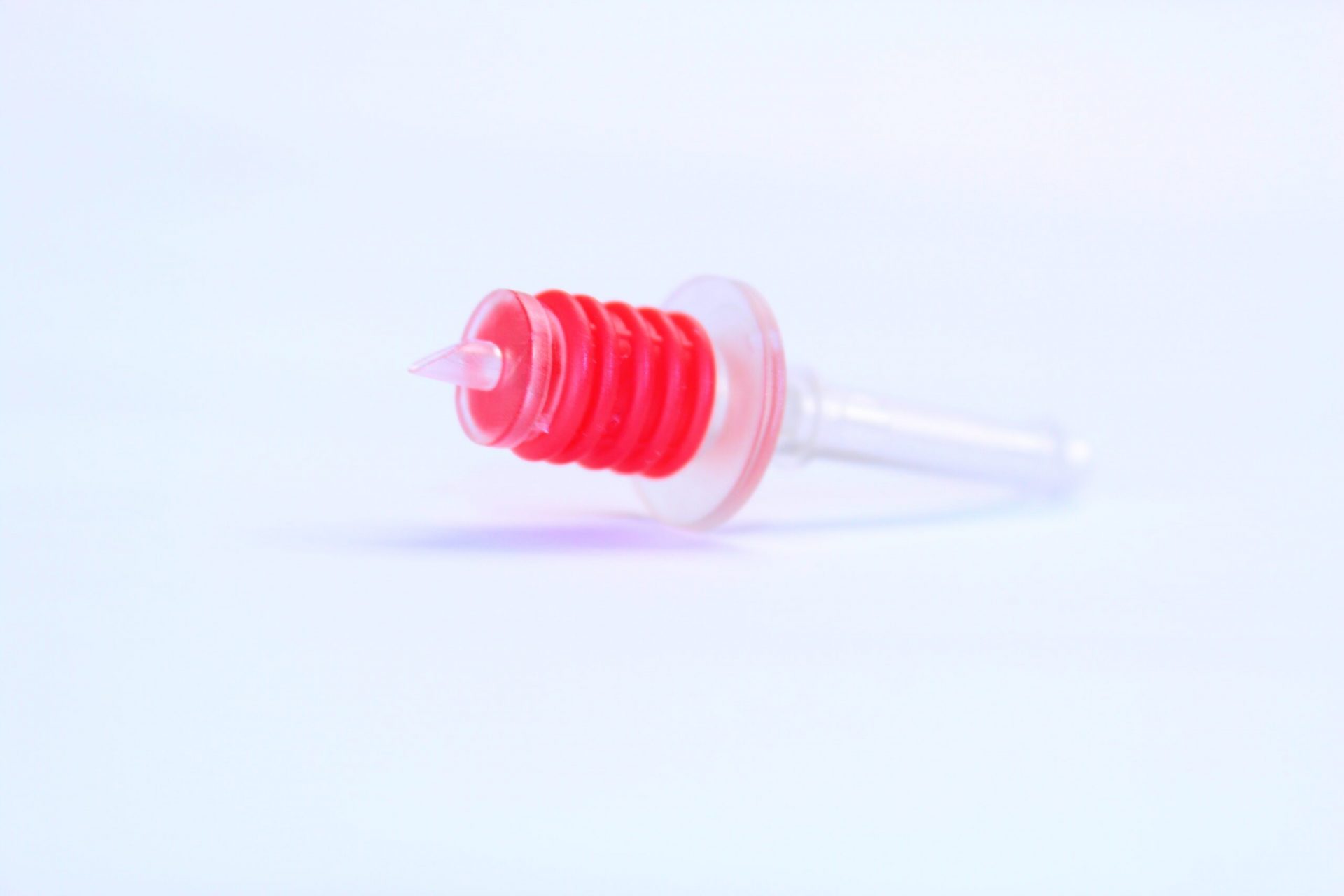
Results: Conducting a proper tolerance stack analysis ensures a syringe will have an appropriate seal. This allows for proper dosing, consistent actuation force, and prevents leakage from the syringe.
3) Achieving Optimal Design
What is optimal design? When designing a product for injection molding, our engineers must consider how to marry manufacturability and functionality. Natech engineers overcome complex part, material and aesthetic concerns to create reliable and high-quality products.
Why is it important? No one wants to spend countless hours designing a syringe for it to be unmanufacturable. Achieving optimal design means that clients can quickly move into production with lower risks of having to make design changes down the line. Without proper design, clients might face slow cycle times, higher labor costs and higher piece prices.
Challenge: A challenge with molding syringes is developing an optimal design that can be injection molded but also meets all the functional and aesthetic requirements of the client. With syringes, the product needs to store and move fluid appropriately, in regard to the volume of the fluid and the necessary speed of fluid movement.
Natech encountered this challenge with a recent client looking to develop a custom syringe. The initial design involved pressing down on a plunger to dispel fluid. However, it allowed the user to press the plunger down so quickly, the fluid would disperse across the tester and showed inaccurate results.
Solution: To address this challenge, our engineers use Design for Injection Molding (DFIM) and Design for Manufacturability (DFM).
Natech made a change to the initial syringe design. Instead of pressing down a plunger, we created a twist syringe. This allowed the user to control the rate the fluid dispelled. This made it easier for the user to twist and disperse fluid through the tip at a more controlled rate, which leads to more accurate test results.
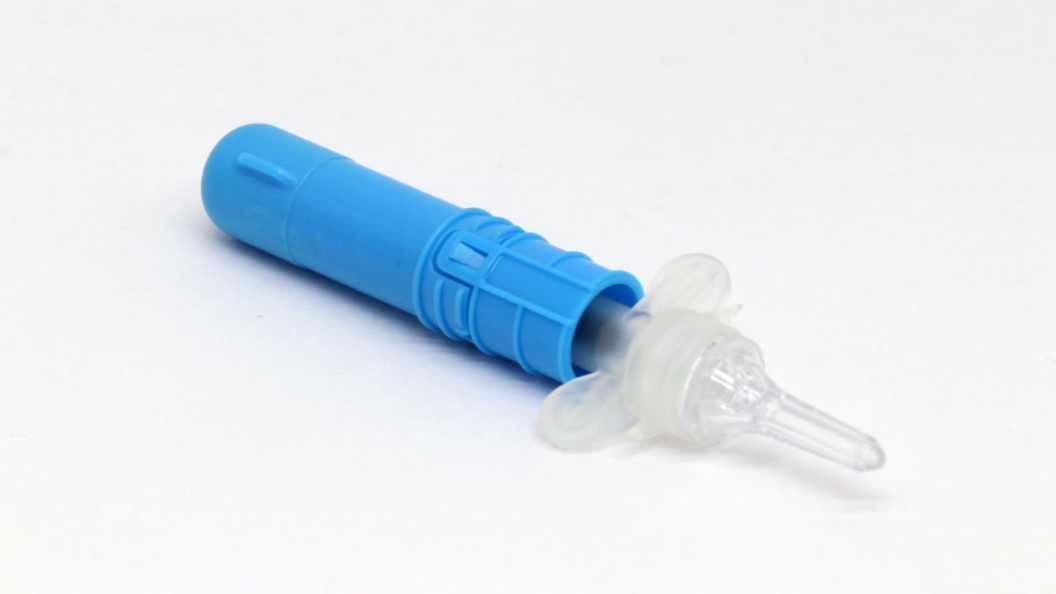
Results: Designing with the constraints of manufacturing in mind ensures engineers consider the product’s end use, part functionality, and how it interfaces with other parts or end users. DFIM and DFM allows final designs to easily transition into manufacture and assembly.
Mold Your Syringe with Natech
Natech specializes in syringe molding and takes pride in the design and engineering efforts that go into creating quality products. To get started on molding your unique syringe application, schedule time with an engineer or request a quote today.