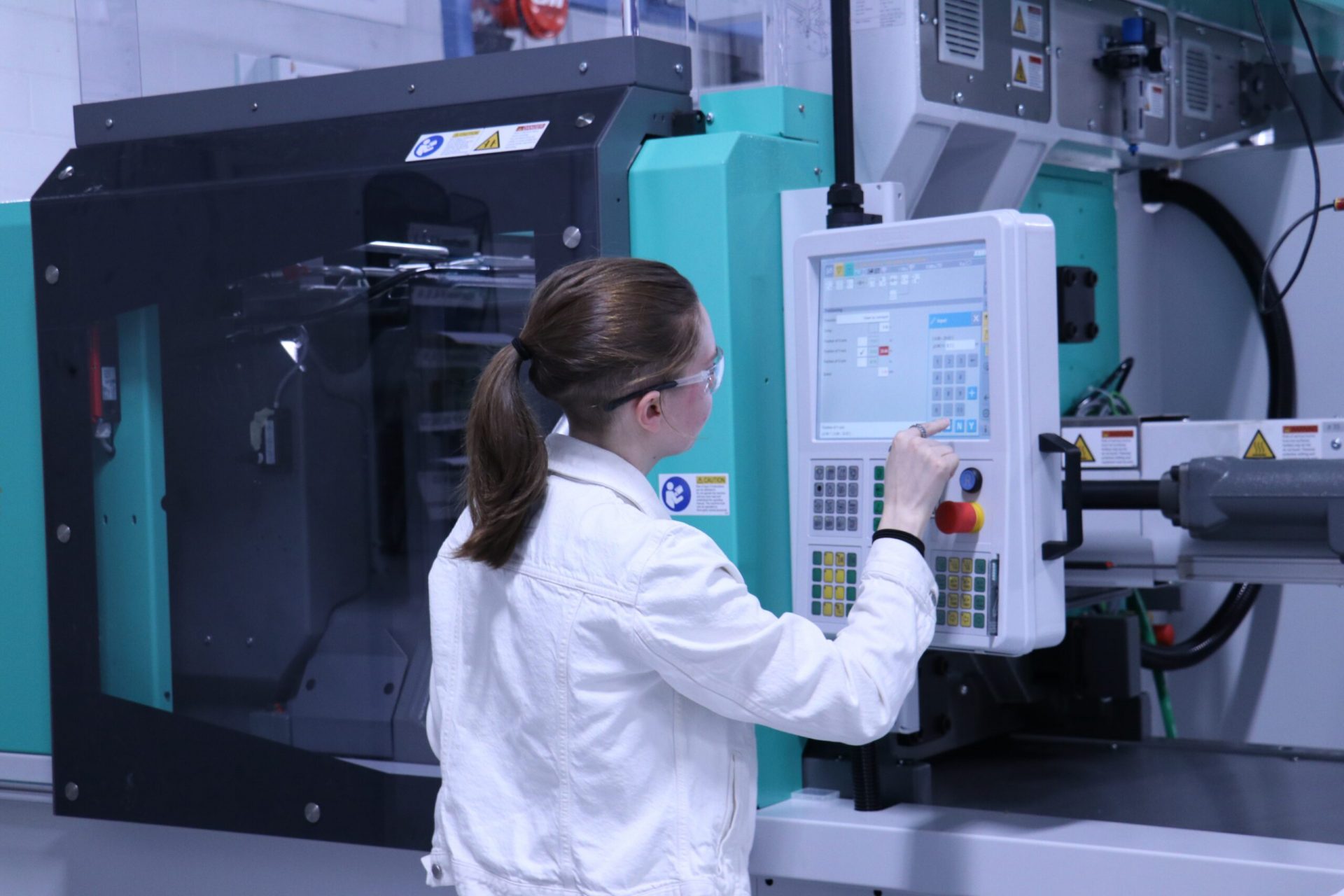
Beginner’s Guide to Design for Injection Molding: Cooling
Learn the Basics of Plastic Injection Molding: Designing for Cooling Success
Table of Contents
- Homepage
- Design for Injection Molding: Filling
- Design for Injection Molding: Cooling
- Design for Injection Molding: Ejection
- Design for Injection Molding: Assembly
- Design for Injection Molding: Inspection
The design for injection molding cooling phase is a crucial step that directly impacts the final quality of the plastic parts. During this phase, the filled plastic in the core and cavity undergoes a cooling process, which causes shrinkage. However, this shrinkage can lead to various challenges such as part deflection, warpage, and sink marks. To address these risks, the design for injection molding must incorporate specific considerations and modifications.
1. Adding Ribs to Part Design
Situation
To mitigate deformation during shrinkage, the design for injection molding incorporates perpendicular walls, known as ribs, as support features. These ribs help limit the distortion caused by plastic shrinkage. However, it’s essential to note that ribs can introduce the risk of creating sink marks on the opposite side of the parent wall.
Solution
To overcome this, the responsible engineer designs ribs with the appropriate parent-to-child wall thickness, striking a balance between structural support and sink mark prevention.
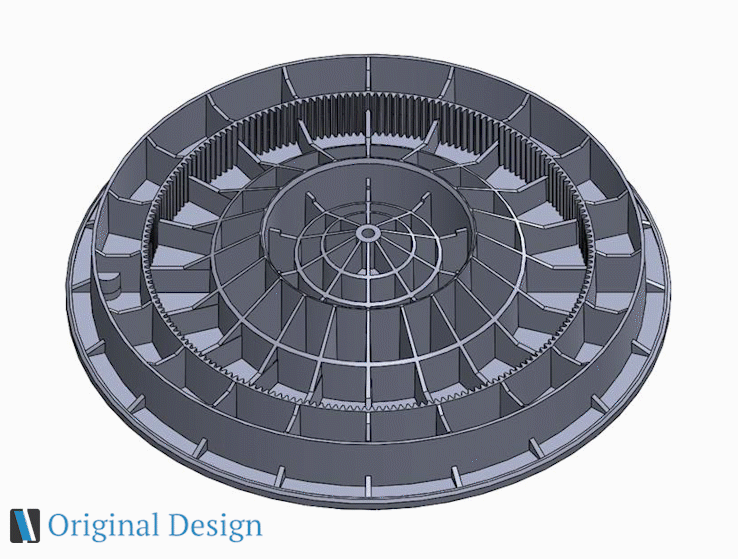
2. Unifying Wall Thickness
Situation
Nonuniform wall thickness in plastic parts poses significant risks to part quality. The transition from thick to thin walls can cause premature cooling, resulting in incomplete filling of the core and cavity, leading to non-fills and short shots. Moreover, nonuniform walls contribute to part deflection, which can negatively impact both functionality and aesthetics.
Solution
To mitigate these risks, the design for injection molding aims to achieve a uniform wall thickness throughout the part. This includes incorporating coreouts where feasible, ensuring functional requirements are met while minimizing injection molding risks.
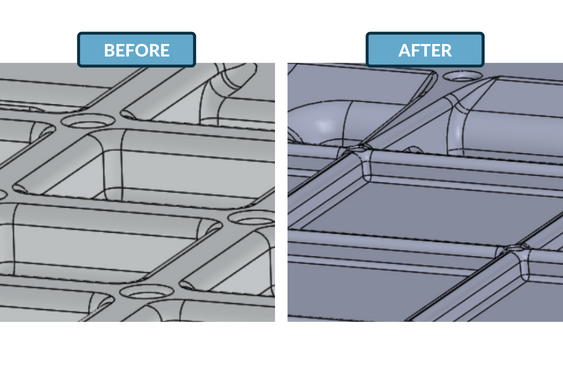
Ensure Success During Manufacturing
The design for injection molding cooling phase is vital for achieving high-quality plastic parts. By incorporating ribs for support and ensuring uniform wall thickness, the risks of deformation, sink marks, and part deflection can be minimized.
Natech specializes in design for manufacturing and injection molding, and our team of experts will help you optimize your designs for the cooling phase. Contact us today for exceptional results in producing exceptional plastic parts.
←Previous Post ㅤㅤㅤㅤㅤㅤ Next Post→