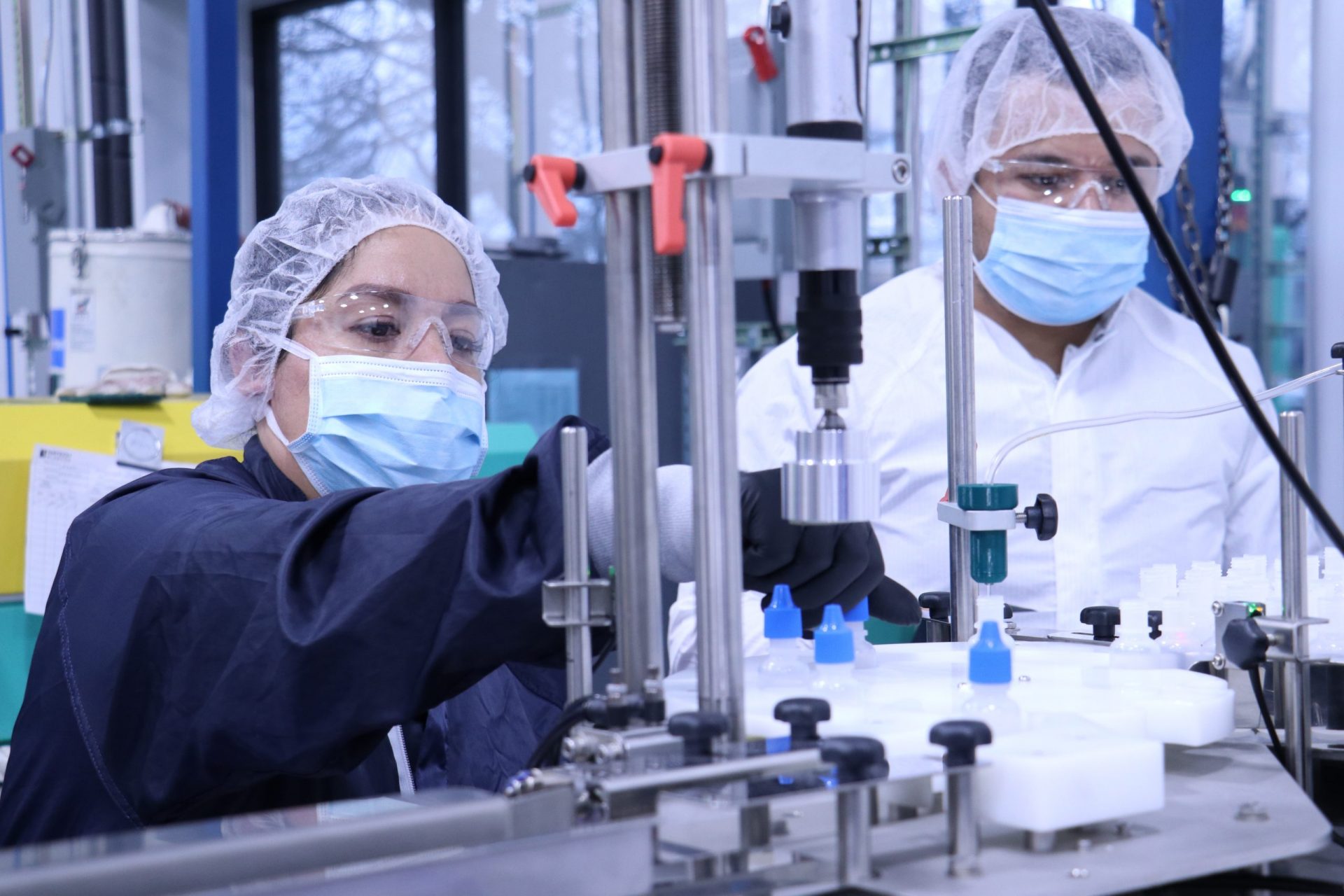
Beginner’s Guide to Design for Injection Molding: Assembly
Learn the Basics of Plastic Injection Molding: Designing for Assembly Success
Table of Contents
- Homepage
- Design for Injection Molding: Filling
- Design for Injection Molding: Cooling
- Design for Injection Molding: Ejection
- Design for Injection Molding: Assembly
- Design for Injection Molding: Inspection
Designing for assembly is a crucial aspect of the design for injection molding process. The engineer responsible for the design must consider assembly requirements and make adjustments as necessary. Assembly design changes can have a significant impact on part design and the injection molding process itself.
Make sure your manufacturer considers these three practices to ensure your part is properly designed for assembly.
Design for Joining
Joining plays a vital role in the assembly process, involving the connection of multiple components through mechanical, adhesive, heat, or welding methods. Insufficient joins can lead to separation of assembled parts and potential leakage. Design for assembly addresses proper joint design, recognizing that different joining processes require specific joint designs. For instance, joints for ultrasonic welding differ from those for adhesion or compression joining.
Some product designs include more components than necessary, resulting in increased molds, parts, assembly steps, capital investment, quality risks, piece prices, and lead times. To mitigate these issues, the design for assembly engineer seeks opportunities to consolidate multiple components into a single component. Balancing factors such as mold cost, complexity, assembly risk, piece price, and quality risk is essential.
Design for Filling
The filling process involves introducing liquid or solid products into delivery and storage devices or packages. During conceptual design, it is crucial to consider filling one part at a time. Neglecting appropriate headspace and filling tolerances can disregard mass production considerations. This oversight can lead to unnecessary splash and spillage risks when filling at high quantities and speeds.
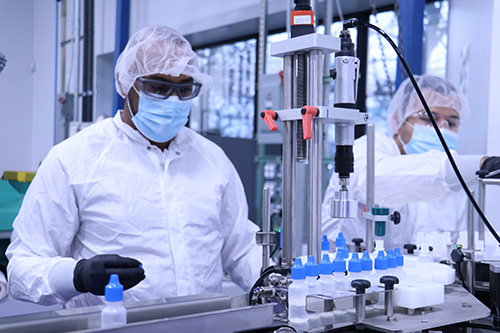
Design for assembly takes into account manual filling and fully automated filling, incorporating filling tolerances and ensuring adequate headspace to limit the risks of splash and spillage.
Design for Sealing
After filling, sealing the device becomes necessary, particularly when containing liquid or solid products. Insufficient seals introduce the risk of leakage, impacting product functionality. The design for assembly process must consider design aspects that affect the sealing surface. Proper ribbing, wall thicknesses, and ejection support are crucial in ensuring even and adequate sealing surfaces.
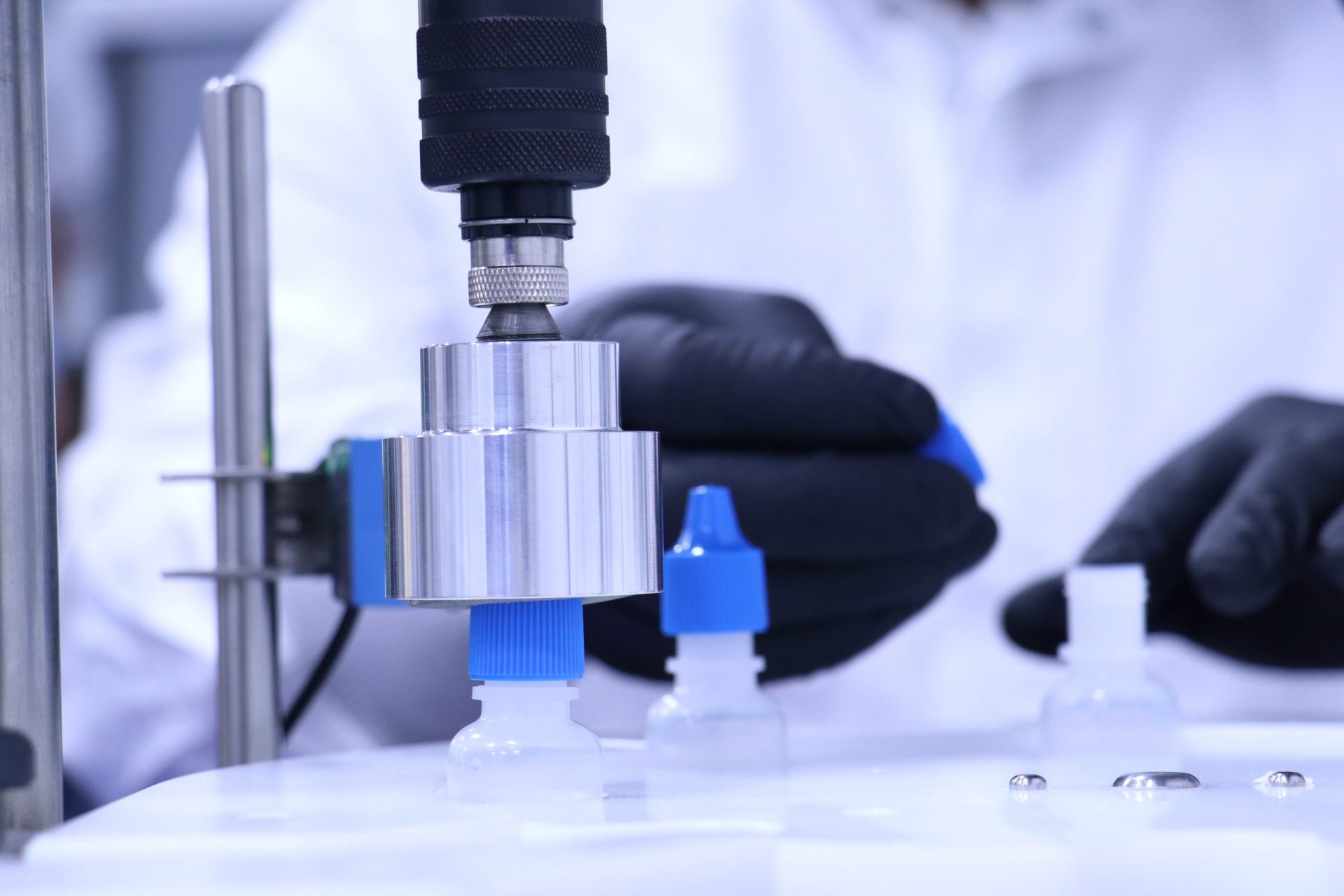
Ensure Success During Manufacturing
Designing for assembly success is a critical part of the design for injection molding process. Manufacturers must consider three key practices: design for joining, design for filling, and design for sealing. Joining processes require specific joint designs, while consolidation of components can streamline assembly. Proper filling considerations minimize splash and spillage risks, and designing for sealing prevents leakage.
Choose Natech for expert assembly design in plastic injection molding. Partner with us to achieve efficient production and optimal product quality. Contact our team today to get started.
←Previous Post ㅤㅤㅤㅤㅤㅤ Next Post→