Enhancing Process Control and Material Selection with an Elastomer and Radial Seal
When our engineers share the challenges that keep them up at night, I’m filled with anticipation rather than worry. You see, I know that these discussions signify deep thinking and problem-solving. Engineers often find themselves navigating the space between theory and practice, bridging the realms of science and manufacturing. The capability of elastomers exemplifies how mechanical engineering, quality engineering, and process engineering interact during the manufacturing process. In this case study, we delve into the application of an elastomer in manufacturing radial seals and explore the critical process control and material selection considerations involved.
Application
A diagnostics client recruited Natech to manufacture a round, elastomer plug that formed a radial seal. The plug would be assembled into the plastic body, which would be molded in COC. The client commissioned single-cavity, steel molds to produce the components.
For the final application, lab technicians would remove the plug, insert the sample, reinsert the plug to form a seal, and shake to mix the fluid sample with highly reactive lyophilized beads.
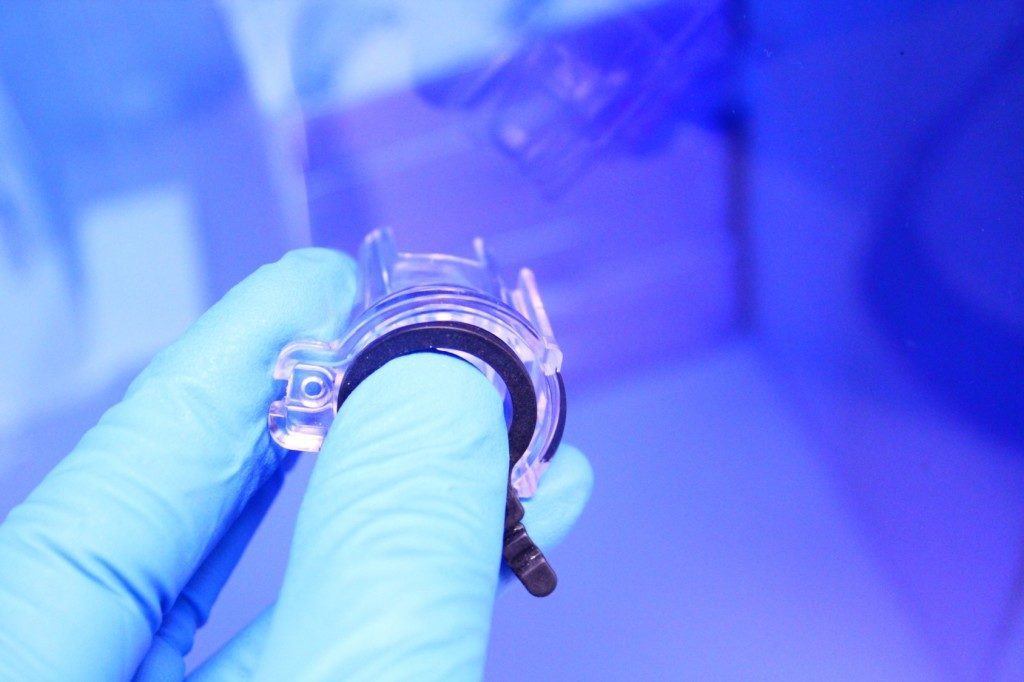
The challenge was to ensure the seal’s integrity during the shaking process, as any compromise could affect the test sensitivity and user safety.
Situation
The elastomeric component, containing a lubricious additive, reacted with the mating COC component during storage and shipping. This caused the parts to stick together, which required forceful removal of the plug and leaving a residue ring that affected seal integrity upon reinsertion.
To address this issue, the client sought our engineers’ support in finding replacement materials. After extensive research, we selected two materials for testing, aiming to establish their process capability. If either material demonstrated a capable process, it would provide a viable option for the client. Otherwise, we would have to explore alternative solutions.
However, assessing elastomer capability posed challenges due to flexibility and out-of-roundness. Measuring seal diameter was complex, with variations based on measurement location and method. Additionally, the material’s durometer and part geometries led to unpredictable variations in out-of-roundness from shot to shot.
It is crucial to interpret the data cautiously, as slight out-of-roundness may not affect the parts’ actual performance. Inaccurate tools or methods could misrepresent process capability or statistical control, leading to unnecessary troubleshooting and time and resource allocation for the client.
Tactic
The Engineers identified three steps necessary to select a replacement resin with an acceptable level of confidence:
- Identify the repeatable measurement method and equipment,
- Confirm the process was in statistical control, and
- Confirm the process was capable.
1. Ensure Repeatability
Our engineers initiated the process by gathering preliminary data. They first used an optical comparator to examine the outer diameter of the seal bump, the contact area with the mating component. However, this method only provided measurements from one projected angle, resulting in varying results based on the part’s orientation and out-of-roundness.
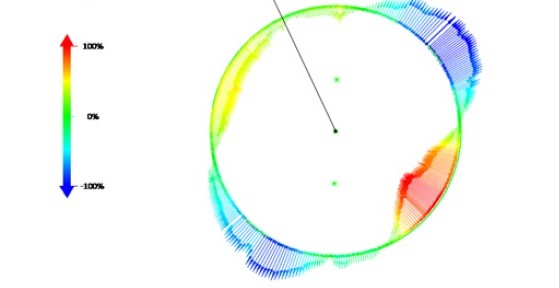
To improve accuracy, we inserted a pin gage into the inner diameter without radial expansion, and retook the optical comparator measurements. Although the variation decreased, significant variability remained.
2. Confirm Statistical Process Control
To verify the process’s statistical control, our engineers conducted a capability analysis of the molding process using the two experimental materials. We calculated upper and lower control limits for parts produced with each material.
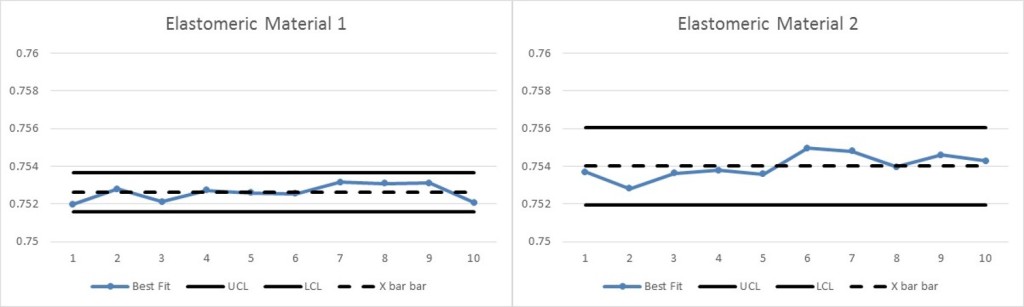
With a sample size of three per subgroup, both elastomers demonstrated statistical control. However, based on a narrower range between the upper and lower control limits, the engineers recommended the first material.
3. Confirm Process Capability
However, being in statistical control does not guarantee capability, particularly when dealing with elastomers’ capability. In this case, the parts’ control limits exceeded the specification limits, indicating precision without accuracy. It’s akin to having excellent aim but targeting a spot away from the desired target.
With molded parts, the solution could involve changing the mold. However, mold modification incurs costs and risks. Therefore, alternative options are explored whenever feasible to ensure the optimal path. In this instance, our team molded the rigid mating component and obtained data on its upper and lower control limits. Considering the worst-case fit, the engineers recommended no mold change to the client. Instead, they proposed adjusting the specification limits to align with the components. The client accepted this approach, resulting in an acceptable fit.
Conclusion
Effectively managing the challenges of manufacturing requires engineers to balance multiple skills. They must distinguish the difference between precision and accuracy and understand the difference between statistical process control and process capability. This case study shows how by implementing a systematic approach to process control and material selection, unnecessary work and problems can be avoided, leading to more efficient manufacturing processes.