Tradeoffs and Solutions for Effective Undercut Design for Manufacturing
Have you ever wondered what challenges keep plastic engineers awake at night? Despite their best efforts, finding the perfect solution without drawbacks can be elusive. In the real world, every solution comes with its own set of risks, forcing them to navigate a delicate balancing act with tradeoffs. Additionally, the realm of plastic engineering is further complicated by the concept of manufacturing with an undercut, which adds another layer of complexity.
One such challenge arises when a part’s functionality depends on an intentional undercut. These undercuts, which often feature snaps, threads, side windows, or horizontal bosses, can latch onto the core side of an injection mold, making clean part ejection difficult. While undercuts can bring immense value to various applications, they also introduce complexity and increased manufacturing costs.
Just imagine the intricate steel formation required to create an undercut, as depicted in the image below. Now visualize the plastic engineer’s predicament: How do they maneuver that steel to extract the part from the mold? Without careful consideration, the part would remain trapped, rendering it impossible to remove.
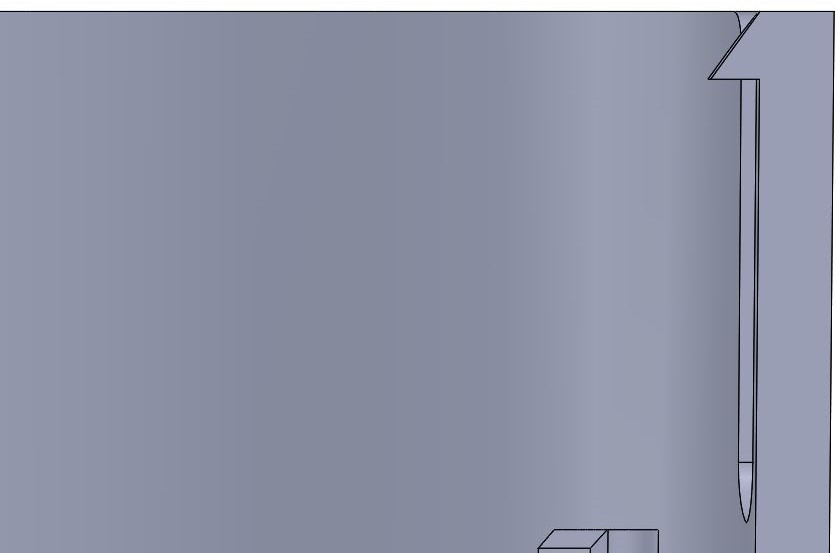
In this case study, we delve into the world of undercuts in plastic engineering, unraveling the challenges faced by engineers and presenting innovative strategies to overcome them.
The engineer’s approach involves careful consideration of both part design and tool design before integrating undercuts. By discerning the role of the undercut at the part design stage, engineers can achieve greater flexibility in its design and implementation.
Moreover, envisioning the part design while keeping the tool in mind enables engineers to skillfully avoid or strategically incorporate undercuts. It is the harmonious interplay of these two factors that allows for accurate evaluation of tradeoffs and the selection of the most suitable solution. To illustrate this concept, we present an insightful case study that sheds light on the importance of this holistic approach.
Application
A medical customer approached us with a specific requirement: the development of an onboard buffer reagent for their diagnostics test. To meet this challenge, our engineer meticulously designed a polycarbonate sample collector that seamlessly fit within a polypropylene buffer storage component.
The primary objective was to ensure the strict separation of the sample and buffer during the collection process. Additionally, it was crucial to achieve a stable assembly lock of the components to guarantee reliable performance. While a hermetic seal was not necessary for this application, minimizing the risk of leakage emerged as a top priority.
Situation
Initially, our engineer devised a subassembly design that relied on a diametric interference fit. However, upon careful evaluation, it became apparent that this design approach carried the potential risk of blood leakage during use. The tight tolerances inherent in this configuration meant that even slight variations could lead to undesirable outcomes, such as the components popping apart or failing to join securely in the first place.
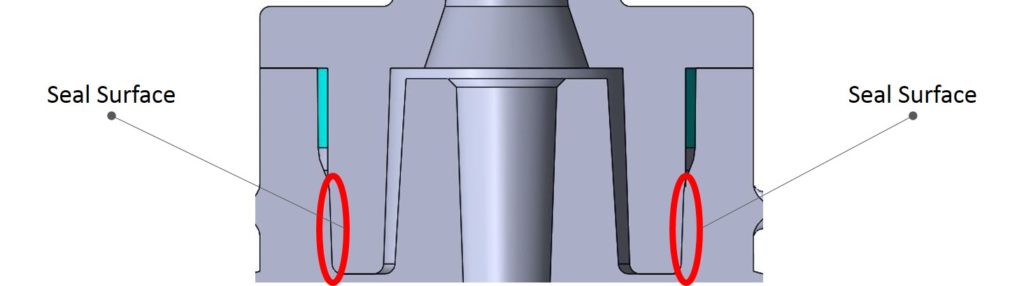
Options
In our pursuit of an effective undercut design, our engineer carefully assessed various options tailored to the unique requirements of the project. By leveraging existing elements within the design, we sought to maximize functionality while minimizing potential limitations.
- Utilizing Cam Functionality: Our engineer leveraged existing cam functionality on the external face of the internal component to incorporate an undercut locking feature. This efficient approach streamlined manufacturing by utilizing existing design elements.
- Exploring Alternative Methods: To form the desired mating undercut on the external component, we considered various options. One possibility was using lifters, angled mold ejection components that form undercuts laterally. However, limited lateral space within the part’s inner diameter made lifters impractical for this project.
- Consideration of Collapsible Cores: Another alternative we explored was collapsible cores, which contract radially to create undercuts during molding. However, space constraints rendered collapsible cores unsuitable for this specific project.
Action
To address the challenges of undercut design, our engineer devised innovative strategies tailored to the specific requirements of the project. Through meticulous analysis and creative thinking, we successfully implemented the following actions:
- Radial Ring Addition: Introducing a radial ring on the internal component created deliberate interference with the external component’s internal face. This interference provided a stable and secure engagement, enhancing overall subassembly performance and functionality.
- Rice Grain Feature Design: Skillfully incorporating rice grain features into the external component’s inner diameter improved grip and engagement. These precisely designed features enhanced both aesthetics and functionality.
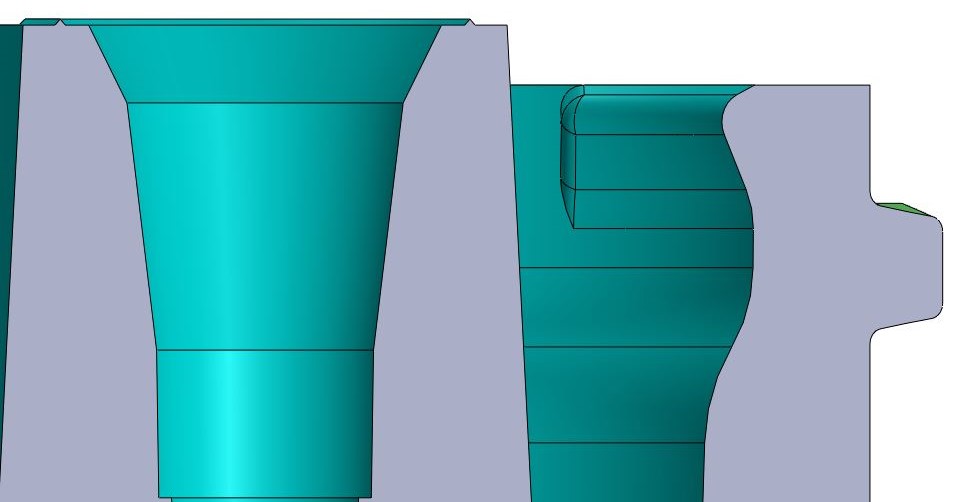
Result
Our engineer successfully minimized leakage risk by implementing strategic design measures. The external component’s material durometer allowed it to eject smoothly without additional mold features, while the undercuts securely gripped the radial ring of the mating component, ensuring reliable engagement.
Undercuts offer valuable functionality and are a deliberate design choice that can be made before the manufacturing process begins. However, their incorporation requires careful consideration of both part and tool design. By exploring various options and considering the tradeoffs involved, you can achieve the best solutions for your product.
We specialize in helping clients scale their products from design to manufacturing, optimizing every aspect, including undercuts. From concept to production, we can assist you in navigating your design and engineering. Contact us for a complimentary design review.