Advantages and Challenges of Each Manufacturing Process
As the demand for new and innovative medical products continues to grow, product developers are seeking manufacturing processes that can produce high-quality devices. CNC machining has long been a reliable method for producing precise components and small quantities of similar parts. However, when it comes to production of medical devices, clients must consider alternative processes, such as injection molding. Injection molding offers different benefits for producing identical parts, making it an appealing option for product developers who are looking to efficiently manufacture their devices.
When it comes to manufacturing your product, choosing the right process is essential. Both CNC machining and injection molding offer distinct advantages and disadvantages, making it important to evaluate which is best for your project’s specific needs. Keep reading to learn more about these processes and determine which is the right fit for your project at its current stage.
What is CNC Machining?
CNC machining is a process used to produce high-precision components and parts. CNC machines use computer aided design (CAD) and computer aided manufacturing (CAM) software to control the movement of cutting tools to shape material into a desired form. While CNC machining is known for its high precision and flexibility, it has limitations when it comes to scaling up manufacture.
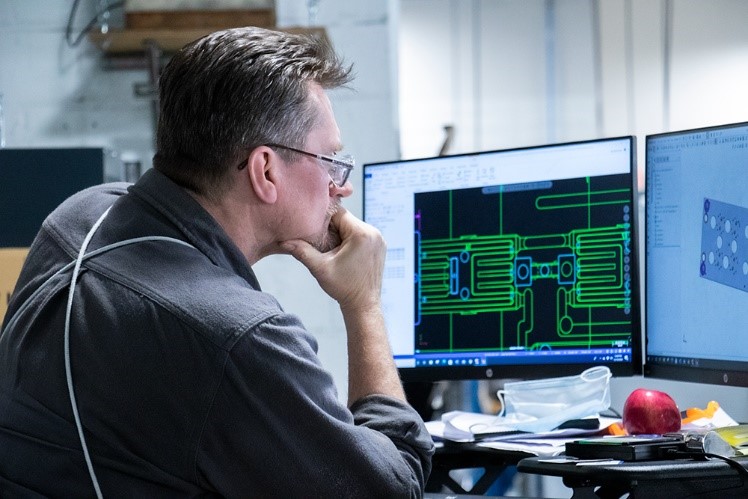
Pros and Cons of CNC Machining
Lead Time & Cycle Time:
CNC machining allows for faster prototyping and iterative design changes. Since CNC machining doesn’t require dedicated molds, changes can be made quickly and easily without long lead times or significant costs.
However, the cycle time for CNC machining can be longer than injection molding, as each part needs to be individually machined. Cycle time varies greatly from part to part depending on the geometry. For an average part, cycle time is about five minutes.
Cost-effectiveness:
One advantage of CNC machining is that there is no capital expenditure associated with an mold for the part. CNC machining also allows for more rapid testing of new design iterations without the need for a mold design change. Additionally, because CNC machining does not require a mold, it can be a more economical solution for companies that need to produce a smaller number of parts.
However, CNC machining is typically more expensive than other manufacturing processes on a per unit basis. The cost per part for CNC machining depends on multiple factors, such as material type being machined, design complexity, part size, tolerancing, time required to produce the part, and other incorporated costs.
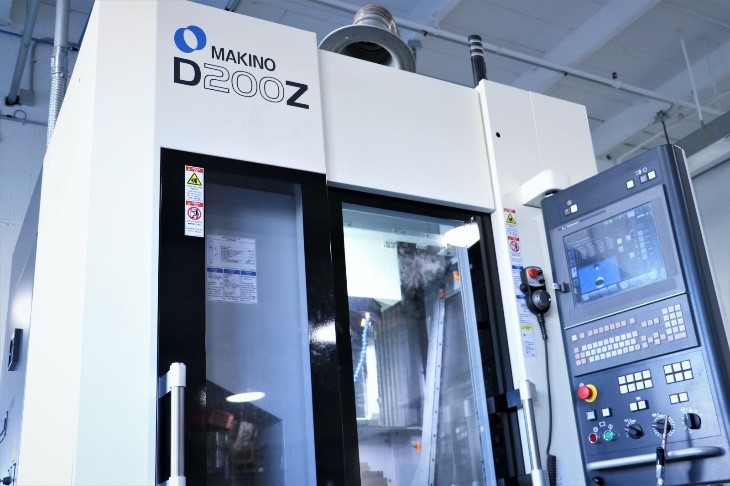
Volume of Production:
Machining parts is suitable for producing low to medium quantities of parts with high precision, typically ranging from one to thousands of parts.
However, it becomes less cost-effective as volumes increase due to longer cycle times and higher tooling costs.
Quality and Reliability:
CNCing is known for producing high-quality parts with high precision and excellent surface finish. To reduce the risk of human error and inconsistency, many CNC machines now incorporate advanced software and automated features that help ensure accurate and consistent production.
However, the quality and reliability of CNC-machined parts can still be impacted by factors such as machine maintenance, operator skill level, and design issues. These factors can lead to issues that can compromise the final product’s functionality. It’s crucial to work with an experienced manufacturer that knows how to carefully monitor and control the process to ensure that parts meet the required quality standards.
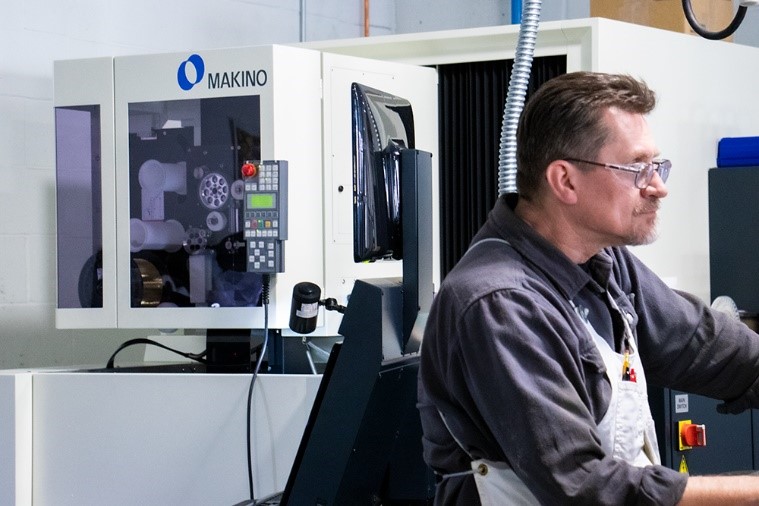
What is Injection Molding?
Injection molding is a process used for producing large quantities of identical components. The process uses a mold that shapes material into a desired form. The mold is usually a steel or aluminum tool and can be used repeatedly to produce various quantities of parts.
Pros and Cons of Injection Molding
Lead Time & Cycle Time:
Injection molding is much faster than CNC machining and can produce parts in a matter of seconds. This increased speed of production leads to faster time-to-market and improved cost-effectiveness, making it a solution for medical device manufacturers who need to meet tight deadlines and have demanding production schedules.
However, all injection molded parts require that you build a mold for the part. The lead time for molds can be anywhere from 3 weeks to 18 weeks, depending on the construction of the tool.
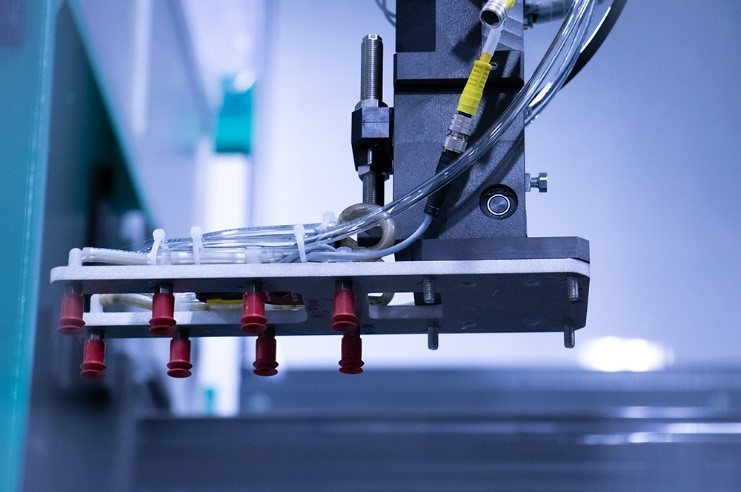
Cost-effectiveness:
One advantage of injection molding is that it has a lower unit cost for production. Injection molding is a cost-effective solution for mass production, as the cost per part decreases as the number of parts produced increases.
However, the initial investment in tooling and equipment can be high, which can make it less suitable for small-scale production. The tooling cost may also prevent product developers with limited budgets from getting started.
Volume of Production:
Injection molding is capable of producing high volumes of parts quickly and efficiently. This is perfect for for medical device manufacturers who need to produce hundreds to thousands to millions of parts in a short amount of time.
However, it’s not always a cost-effective solution for smaller production runs. Since injection molding often requires the creation of custom molds, the initial setup costs can be relatively high. This means that for smaller production runs, the cost per part may be higher compared to other manufacturing methods.
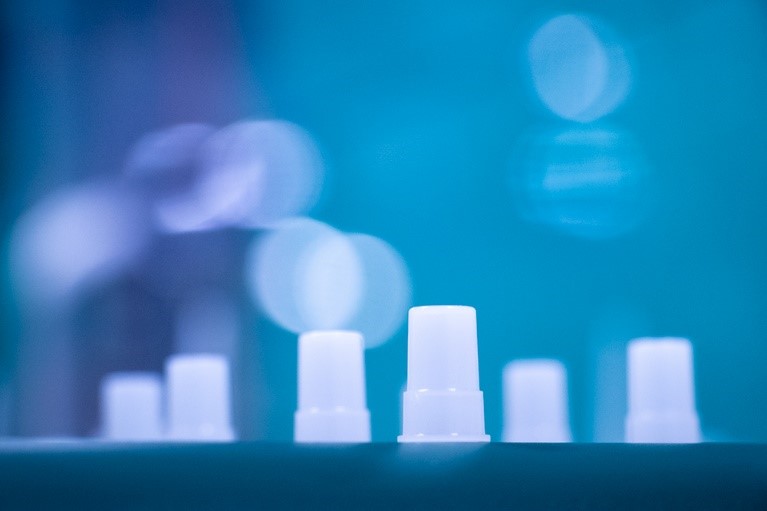
Quality and Reliability:
Injection molding is a highly efficient and cost-effective manufacturing process that provides exceptional quality and reliability. The use of computer-controlled systems and advanced manufacturing techniques ensures that the finished products are of consistently high quality and meet strict industry standards. Additionally, injection molding allows for tight tolerances and complex geometries that are difficult or impossible to achieve with other manufacturing processes. Injection molding produces parts with high precision and excellent surface finish, which results in high-quality and reliable final products.
Nevertheless, it is crucial to partner with a reputable and experienced injection molder to ensure that the final product meets all the required quality and performance standards. A reliable injection molder will have strict quality control measures in place, ensuring that every product that leaves their facility is consistent and reliable.
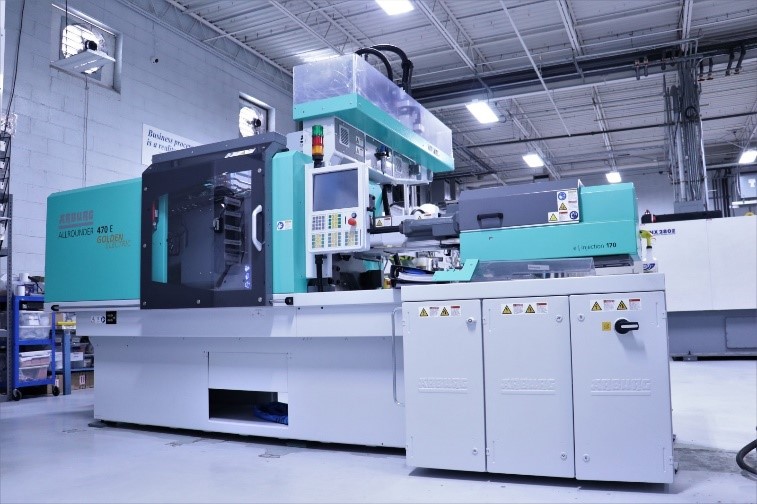
Conclusion
In conclusion, both CNC machining and injection molding offer advantages and challenges for product developers in the medical device industry. CNC machining is a great option for small quantities of parts or for producing high-precision components, while injection molding is ideal for mass production, producing complex geometries and shapes, and accelerating time to market.
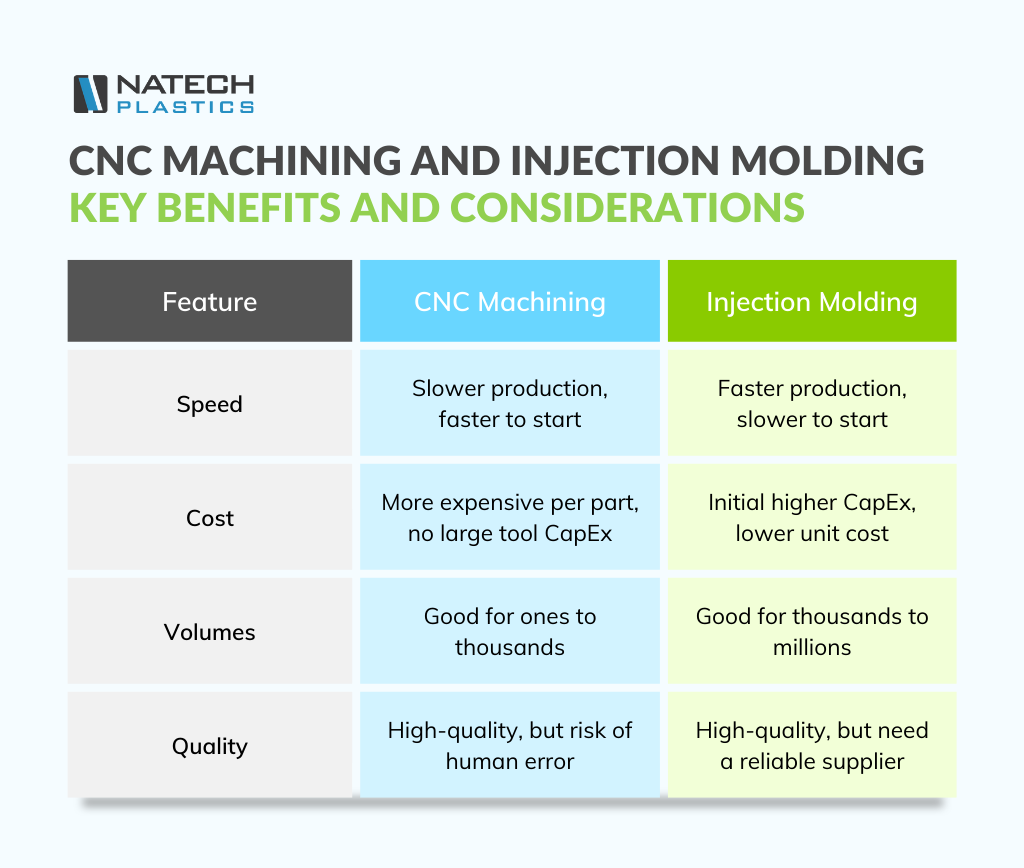
Each process has its own set of pros and cons related to factors such as cycle times, costs, and part volumes. Ultimately, choosing the right manufacturing process will depend on the specific needs of the product and production goals. It’s important for product developers to carefully consider these factors before making a decision and to work with experienced and reliable manufacturers to achieve a high-quality final product.
At Natech, we offer both CNC machining and injection molding services to help our clients meet their manufacturing needs. Whether you’re in the early stages of product development or ready to scale up production, we have the expertise and technology to bring your medical device to market. We want to make sure that you’re using the manufacturing method that’s right for you. Contact Natech to determine which process is best for your project.